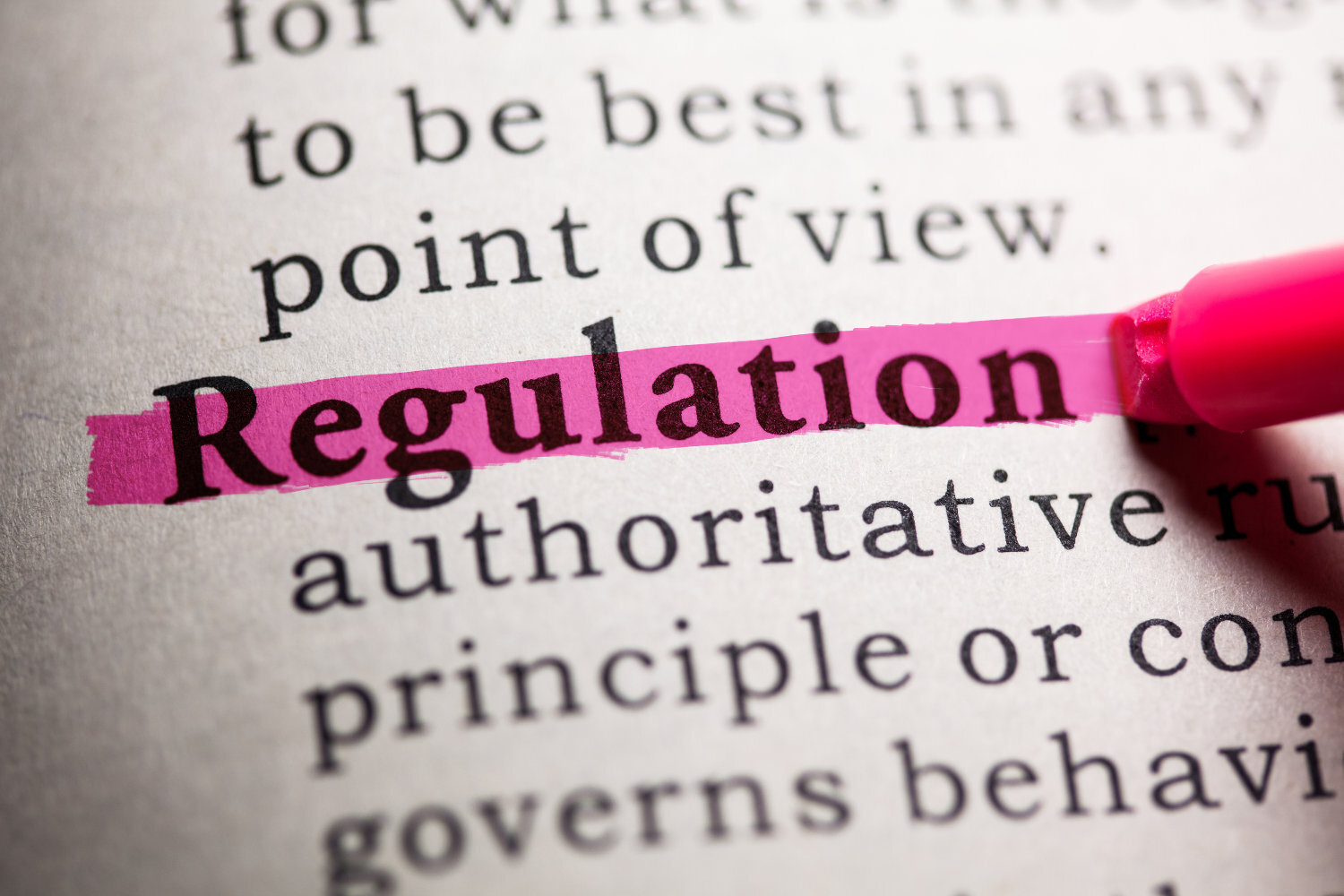
Airtightness in Irish Building Regulations
This is Part 1 covering essential building regulations for energy efficiency & comfort in the Republic of Ireland.
The second part of this blog series covers the risks of condensation and weathering.
Control of airtightness for energy efficiency & comfort
Ireland finds herself on the western fringe of the continent. Located here, she suffers the full force of whatever meteorological delight the North Atlantic cares to deliver. Perhaps this consistent ‘weather’ is why Irish building culture is so strong. The general Irish public is quite well informed about building efficiency & quality. Self-builders, building control and occupants alike will expect high quality from their homes and buildings. Airtightness is a corner-stone to achieving high comfort.
As a builder, you will, therefore, want to meet these high expectations, and you must also ensure you have complied with the minimum building regulations.
This blog post is your reference guide to getting to that point.
Document L; Dwellings; New build
The technical regulations
In the following, we’re referring to the Technical Guidance Document L for dwellings 2017 (note: since the publication of this post a new 2019 version of TGD L for dwellings has been published with a tighter airtightness target of 5 m3/hr/m2, along with other changes).
Requirement L3 & paragraph 1.12 require an EPC calculation to be given to building control and the client prior to completion. EPC is a measure of building efficiency. It is calculated for each individual dwelling and must meet national and local minimum performance standards, such as planning guidance.
The EPC cannot be greater than the Maximum Permitted Energy Performance Coefficient (MPEPC) of 0.4; Maximum Permitted Carbon Performance Coefficient (MPCPC) is 0.46. With the NZEB requirement incoming by 31 December 2020, these values will be improved further; to 0.3 and 0.35 respectively. The air permeability of the building fabric (in m3/hr/m2@50Pa) will have been entered into an early stage DEAP calculation & will be in the building specification.
This value is the mandatory requirement that you must meet.
Important: You need to know what that value is & how difficult it is to achieve it on this job.
If you need help on this we’re happy to help & answer your questions!
Contact SIGA nowThe impact of NZEB on airtightness
With the introduction of the NZEB standard for new buildings in the ROI, the method of demonstrating compliance will not change. It is the performance targets that are becoming tougher. This means you need to manage the risk of failing the air test all the more closely.
Below is a summary of the requirements and an example of the improvement required to airtightness.
Currently | NZEB | |
---|---|---|
Domestic new build | 25-30%better | |
Maximum Permitted Energy Performance Coefficient (EPC) | 1 | 0.3 |
Maximum Permitted Carbon Performance Coefficient (CPC) | 1.5 | 0.35 |
‘Likely compliant air permeability m3/hr/m2@50Pa | 5 | <3.5 |
Non-Domestic new build | 50-60% better | |
Maximum Permitted Energy Performance Coefficient (EPC) | 0.4 | 0.3 |
Maximum Permitted Carbon Performance Coefficient (CPC) | 0.46 | 0.35 |
‘Likely compliant’ air permeability m3/hr/m2@50Pa | 5 | 3 |
Controlling air leakage
Section 1.3.4 calls for ‘reasonable provision to control air leakage’, i.e.:
(a) identify the primary air barrier elements, (e.g. sheathing, plaster, vapour control layer, breather membrane) at early design stage;
(b) develop appropriate details and performance specification to ensure continuity of the air barrier. Communicate these to all those involved in the construction process. Responsibility for construction of details should be established;
(c) provide on-site inspection regime and related quality control procedures so as to ensure that the design intention is achieved in practice. This is developed a little in 1.5.2.1.
Extra tip: It is important that you are familiar with the relevant Acceptable Construction Details within “Limiting Thermal Bridging and Air Infiltration – Acceptable Construction Details”.
Testing for airtightness
We recommend testing twice. Firstly at the completion of the airtightness layer (usually as soon as the windows have gone in), yet before dry lining/plastering.
We suggest testing again when the fit-out is completed. Complex buildings will need further tests. In all cases, testing should be performed on building completion.
So how do you test air permeability on-site? 1.5.4 describes the procedure for testing.
Do you need any additional guidance on the testing procedure? Check out these links;
- Airtightness Testing for New Dwellings by BSRIA Airtightness
- TM23: Testing Buildings for Air Leakage by CIBSE
- Technical Standard L2. Measuring Air Permeability of building envelopes (Non-Dwellings) by ATTMA
Does every dwelling need testing?
Not necessarily, although there is a benefit in doing so. Document L, 1.5.4 Table 4 defines the minimum extent of testing.
NB 1.5.4.7 requires a test on every dwelling that claims better than the mandatory standard of 7 m3/hr/m2@50Pa.
Why does any of this matter?
Well, if a building fails to meet what’s in the DEAP calculation, it must be fixed and retested until it does. This can cause serious cost & delay. If it can’t be improved, the calculation should be amended. So, poor performance can mean that the building fails building control, is severely delayed, or fails to meet the contract requirements. This should be a very strong motivator to aim to exceed the stated airtightness target.
What’s more, poor airtightness leads to issues with condensation.
The best buildings aim for zero and accept a tiny tolerance as their target. As Mark Siddal from LEAP likes to illustrate the equivalent leakage area of some of his Passivhauses, when added up across the whole building, is less than a 10 cent coin!
So, we have covered new housing, how is it different for renovations?
Document L; Dwellings; Renovation
In the following, we’re referring to the Technical Guidance Document L for dwelling 2017.
Paragraph 2.1.4 gives guidance on existing dwellings. Similar procedures as for new builds are required.
Specific guidance is given for improving airtightness in existing dwellings; Diagram 3 in the document illustrates this:
a) sealing the void between dry-lining and masonry walls at the edges of openings such as windows and doors, and at the junctions with walls, floors and ceilings (e.g. by continuous bands of bonding plaster or battens);
(b) sealing vapour control membranes in timber-frame constructions;
(c) fitting draught-stripping in the frames of openable elements of windows, doors and rooflights;
(d) sealing around loft hatches;
(e) ensuring boxing for concealed services is sealed at floor and ceiling levels and sealing piped services where they penetrate or project into hollow constructions or voids.
These approaches are relevant to using the plasterboard as the vapour control barrier, which is not something we would advocate.
The illustrations in the approved document B5 and B6 present typical wall and roof build-ups. Below we interpret these with a highlight of the preferred location of vapour control & airtight layer (red dashed line) and wind/weatherproof membrane (blue dashed line).
Check out the main types of vapour control layer in this blog post.
So that is new and renovated dwellings wrapped up. How are non-domestic buildings dealt with?
Document L; Non-Domestic Buildings, New Build
In the following, we’re referring to the Technical Guidance Document L Buildings other than Dwellings 2017.
The principles and approach are very similar for Non-domestic as they are for Domestic.
Schools, swimming pools, archives are examples of non-domestic buildings which will require extra-special attention to airtightness for efficiency or comfort.
Requirement L5 & paragraph 1.12 requires an EPC & CPC calculation to be run using NEAP. The EPC & CPC are a measure of building efficiency. It is calculated for each individual building and must meet national and local minimum performance standards, such as planning guidance.
The NEAP should be no greater than the Maximum Permitted Energy Performance Coefficient (MPEPC) of 1. Maximum Permitted Carbon Performance Coefficient (MPCPC) of 1.5.
With the NZEB requirement incoming by 31 December 2020, these values will be improved to 0.3 and 0.35 respectively.
Read more about NZEB in Ireland
Read moreThe air permeability of the building fabric (in m3/hr/m2@50Pa) will have been entered into an early stage NEAP calculation http://www.seai.ie. & will be in the building specification.
This value is the mandatory requirement that you must meet.
Typical values for air permeability
The unit of measurement is m3/hr/m2@50Pa. In words that is ‘what is the total rate of air leakage (in m3/hr) divided by the total area of the external envelope (in m2), when the dwelling is pressurised to 50 Pascals above ambient.
A high value means high permeability, i.e. poor performance.
m3/hr/m2@50Pa | |
---|---|
Maximum value (worst allowed) | 7 |
Typical for a new dwelling with trickle ventilation | 5 |
Likely compliant performance, as per appendix E | 5 (Domestic) |
“Reasonable upper limit” | 5 (Domestic) |
Typical for a new dwelling with MVHR | <5 |
NZEB likely compliant | <3.5 |
Best practice, Passivhaus* | 1 to 2 |
Paragraphs 3.14-3.22 describe the testing procedure, which references ATTMA technical standard L1.
*Be careful with units. Passivhaus specifications are often stated in Air Changes per Hour (ACH) at 50Pa, which is different and can be converted only if you know the building measurements.
Document L; Non-Domestic Buildings; Renovations
The technical regulations Technical Guidance Document L -Buildings other than Dwellings 2017 Existing Buildings
Our final category of building is Non-domestic buildings, and their renovation.
Paragraph 2.1.4 gives you guidance on existing dwellings. Similar procedures as for new builds are required.
Specific guidance is given for improving airtightness in existing dwellings:
- sealing the void between dry-lining and masonry walls at the edges of openings such as windows and doors, and at the junctions with walls, floors and ceilings (e.g. by the use of certified air tightness tapes and/or membranes);
- sealing vapour control membranes in timber-frame constructions;
- fitting draught-stripping in the frames of openable elements of windows, doors and rooflights;
- sealing around loft hatches;
- ensuring boxing for concealed services is sealed at floor and ceiling levels and sealing piped services where they penetrate or project into hollow constructions or voids
Conclusion
This article is a quick summary of the ROI regulations with respect to air-permeability for efficiency. Guidance on moisture and keeping the weather out is given in Part 2 of essential building regulations in Ireland.
If you are planning to go well beyond the regulatory minimum, as we suggest you should be, do review the further guidance at the end of UK regs Part 1.
Achieving decent airtightness has a reputation as being tricky, but if you take good advice, plan carefully and maintain a quality culture on-site, it doesn’t need to be so.
The route to success is the same for any building:
- Identify the airtightness value you need to achieve
- At the start of the job make a work plan for adapting the design and assembly to ensure success
- SIGA can offer workshops, advice, modelling and warranties to assist you with managing the risk
- Ensure that everyone on site is aware of the target and of the process required
- We recommend a fault-finding test once the windows are in & before dry lining commences. This may require a staged approach
- Allow time for a test and remedial works before practical completion
- If you spend a little extra on quality, easy-apply tapes and membranes that speed up install and reduce risk of failure, we feel that’s a worthwhile investment.
Check out the very end of this article for a rundown of some extra guidance.
If you are interested in further information and help on this topic then.
Anything omitted?
If you think we’ve missed something critical, do please make it known in the comments.
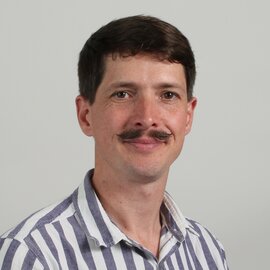
Bertie Dixon
Bertie has practised building services engineering and sustainability consulting in the UK for 15 years. He is a certified PassivHaus planner. He is on a mission to help you deliver a high-quality building, one that does what it says on the tin.