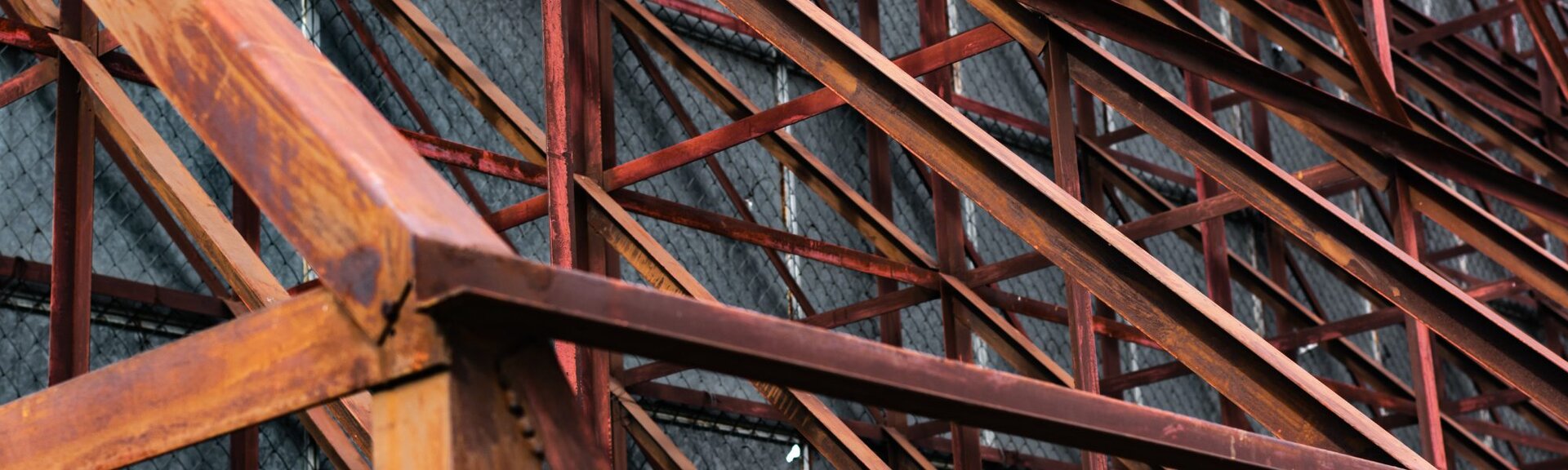
Metal framing; Don’t get wet
Metal framing is light, strong—and thermally conductive. We explain the moisture risks and how to prevent damage, with insights from a real-world case study.
Metal framing in the UK
Heavy gauge steel
For long spans, engineers spec a heavy-gauge steel beam. Typically, contractors of high rise & office developments use a full heavy gauge steel frame.
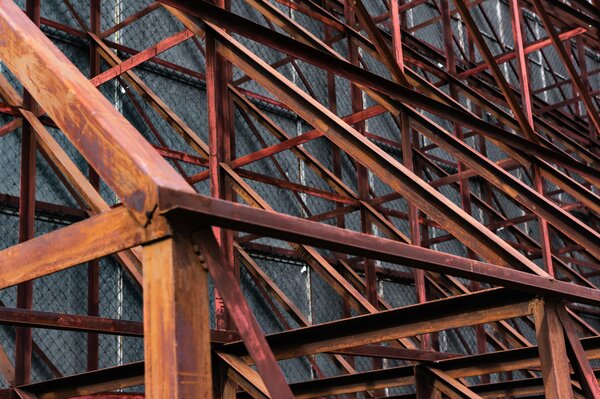
Heavy gauge steel
Light gauge (LG) stud
Light gauge galvanised steel framing, by contrast, is thin-sheet; cold-rolled metal which is used as stud work. Quick, inexpensive and familiar; builders commonly use this for in-fill wall panels. Metsec is one of the most common brands.
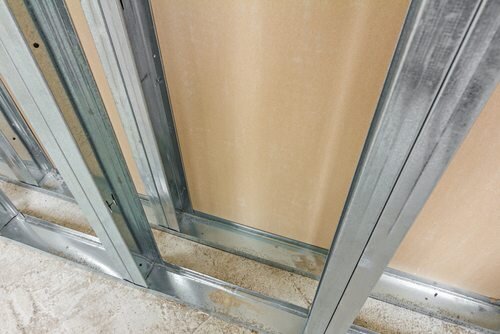
Light gauge (LG) stud
Light gauge structural framing
On some schemes, this light gauge stud is used to build the entire building. It’s known as structural steel framing, or SFS. Metframe is the major brand here. It is a form of modern method of construction (MMC) which can offer time & cost savings onsite.
The detailing of heavy gauge steel framed buildings is similar to other framed buildings. However, LG steel, both structural and non-, requires extra care as it tends to include more metal in the insulation zone. That’s why in this article we focus on light gauge steel.
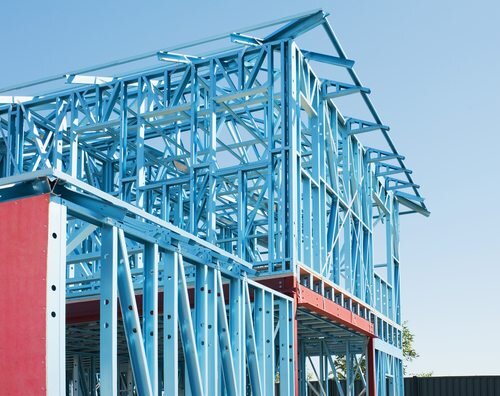
Light gauge structural framing
What’s in a wall?
A typical LG steel stud wall looks like this, from inside to out:
- Plasterboard lining
- ~100mm LG stud forming a cavity for services; fibreglass insulation partial fill
- Cementitious board acts as structural sheathing, fire & smoke separation and as the air & vapour control layer (AVCL)
- A layer of insulation (rigid or rockwool batt)- the thickness depends on target U value. 30-200mm
- Air cavity
- Weathering face; usually brick or rain screen; supported off the LG stud & board
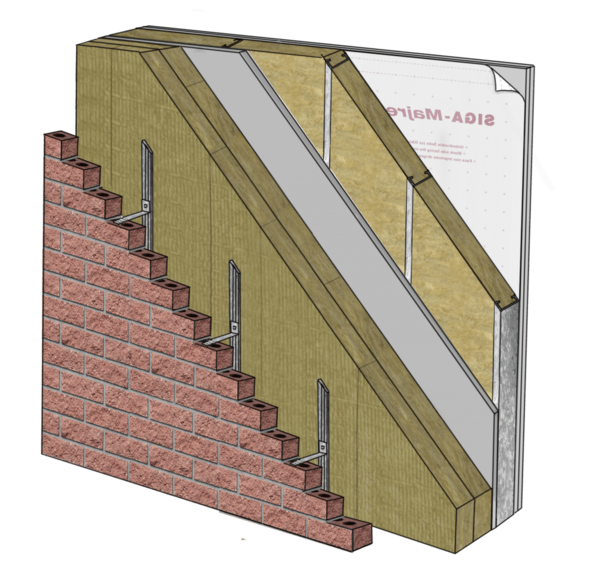
A typical LG steel stud wall
Where’s the risk?
If the air & vapour control layer (AVCL) isn’t continuous, air will flow through and condense on any cold surface in large quantities. Using the cementitious board with taped/sealed edges as the AVCL works well in the above arrangement as its protected, solid & hopefully continuous. For a masterclass in achieving a continuous AVCL, check this out.
Metal in the inner layer
When significant metalwork crosses a layer of insulation, it conducts so much heat that the insulation can be negated. This is happening in the stud layer of the wall above.
But what about the glass fibre insulation in between the studs, I hear you ask? Well that can actually increase this risk of moisture, by limiting warmth from the room.
Metal in the outer layer
That is why the build-up relies on the external insulation to achieve the U value. This insulation is usually either rigid or fibrous batt like mineral fibre. We’ll concentrate on rigid as is most tricky. You need very thick rigid insulation, up to 200mm to achieve a good U value. But this insulation isn’t completely continuous, either.
Look closely and you’ll see that the support system must penetrate the rigid insulation. If the face is brickwork this is so heavy it needs regular & substantial shelf angles, too. These study metal brackets further bridge the rigid insulation. The support system conducts heat out of the board & LG stud. And as the stud is internal to the AVCL, moisture may readily condense on its surface. When the rigid insulation is thicker it requires more support metalwork, hence more thermal bridging. The heat loss via the support system is real but manageable, with a perfect install.
But building is usually not a perfect art. A common issue in this type of wall is the support system which punctures & damages the crumbly rigid insulation & causes it to lift away from the sheathing board. This allows cold air to flow through & behind the boards to negate the effect of the rigid insulation. This effect is less pronounced with squishy mineral wool, but it can still occur without careful installation.
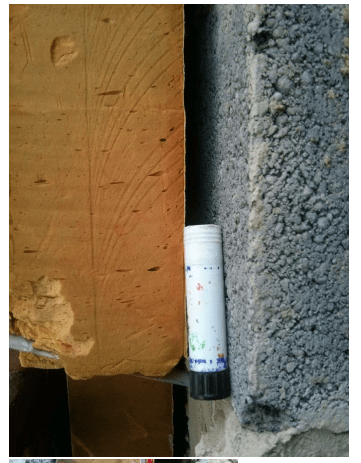
Poor quality installation. Although this example is in a brick & block wall, the same issues can occur with rigid insulation in a partial fill cavity on any building site.

Rigid insulation is hard to do well; this insulation may as well not be there. This example is in a brick & block wall, the same issues can occur with rigid insulation in a partial fill cavity on any building site. Pritt Stick for scale
Small bits of metal can make a big difference
Whatsmore, seemingly small metallic details can make a large difference. Building Physicist Nick Devlin modelled a rainscreen curtain wall. If he ignored the two metal screws in the calculation (as they often are) the heat loss is underestimated by 15%. Perhaps you could say the Devlin the details.
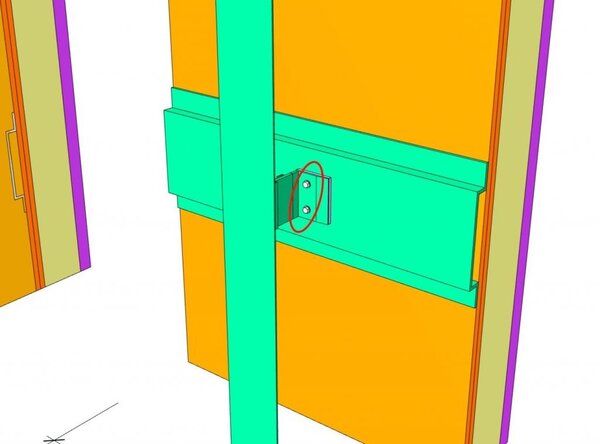
The effect of metal in the insulation zone; if the two screws circled are ignored the heat loss is significantly undersized Picture: Fabric Building Physics
Structural SFS
In the case of structural SFS, the framing is holding the whole building together, so there’s more metal in the insulation zone. So, we must manage this heightened risk.
In writing this article we chatted with Toby Cambray at Greengauge, another experienced building physicist. He confirms:
“Even if the support system is well resolved, tricky details can arise on site, especially around windows and balconies, which can lead to problems down the line, if not considered properly.”
Well insulated walls are not the only issue. In a wall with a high (worse) U value of 0.3 W/m2.K, the rigid board might only be 30mm thick. In this case, the stud is barely insulated, so condensation is highly likely to form in cold weather.
In summary, with a poorly conceived or assembled wall, you risk the U value not being achieved, or a gap in the AVCL. The resulting moisture build up can lead to ill health or in extreme cases structural failure. The suppliers of the LG stud, masonry support and insulation should be your first port of call for advice on how to limit this.
So, how do we sort this out?
“For moisture-safe construction we need to stop mass air flow, and limit the thermal bridging.“
Stopping mass air flow
As a general principle, the AVCL should be on the warm side of the insulation. You might be tempted to use the plasterboard as the AVCL. This can be a recipe for disaster. For example, it requires your electrician to perfectly seal every single penetration by the services, which is very challenging to deliver in practice. Also during occupation, any time the resident puts up a shelf or a picture, they could jeopardise the integrity of the AVCL layer. Not robust enough.
A better solution is to introduce a service cavity behind the plasterboard and place the AVCL on the internal face of the stud. The AVCL could be a membrane, or a board, or both. The joints should be well sealed. This would prevent mass air flow, prevent moisture risk and provide your air tight layer. The outer sheathing board is likely still required, for fire reasons. The cost of this approach is an increased wall depth, which isn’t as efficient as it might be.
Limiting the thermal bridging
There are a number of arrangements available that might limit the creation of cold spots in the wall. A double LG steel stud, or cross-battened stud arrangement, would further separate the layers, with the ability to thermally isolate each layer. However, in doing so we have introduced more cost, more faff and we have not completely solved the bypassing effect of the metal around the insulation.
Alternate materials can give a better performing solution. Although timber studs are physically larger, they are significantly less conductive than metal. A Larssen truss or I-Joists provide support in a slimmer profile, but timber may not suitable for all situations, especially high rise.
Lightweight concrete blocks, of clay or cement-based, supported by a concrete frame, can avoid the need for a vented cavity altogether. The cavity can therefore be filled with loose fill insulation which will solve much of the issues raised above. This is how we support the brick with far less bridging, to achieve a more robust arrangement overall. The designers used this solution on Agar Grove 1A, a new build Passivhaus apartment building in London.
Case study, Wilmcote house
Let’s take a look at another real-world example. There are far more unknowns in renovation than in new build. Renovations built to EnerPhit standard, have to perform extremely well in practice. James Traynor at ECD Architects talked us through how they used LG steel stud in a considered way to overclad a 1970s block of flats at Wilmcote house in Portsmouth. The target U value was 0.15W/m2.K, although James feels that the result bettered this due to the additional loose insulation installed in the tolerance zone used to accommodate the uneven face of the existing building.
In summary, they achieved an airtightness, N50 of 1 like this:
- The dedicated AVCL membrane is located at a depth of 100mm into the wall, so it is protected from damage.
- The membrane is mounted onto a ply board, for support & buildability
- A self-supporting LG steel frame was constructed outside the existing wall to hold the retro-fit insulation. The frame is tied back to the building. Tie penetrations are made good.
- Careful detailing, collaboration, training onsite & testing managed quality.
They limited condensation risk on the metal studs with;
- A carefully detailed & installed internal AVCL limits mass air flow
- A continuous & uninterrupted outer wrap of 100mm Rockwool keeps all metalwork reasonably warm
- The structure builds up in three distinct layers; to reduce bridging.
- Soft insulation is much more workable than rigid; it is easy for installers to plug all the gaps to prevent internal air flows.
Check out this video made by BRE which provides some detail on how they addressed the thermal bridging & build-ability issues. You can find more information here .
Summary
If you’re going to use metal frame be aware of the risks. Avoid nasty surprises later down the line by
- Following the manufacturer’s recommendations,
- Limiting mass air flow with a continuous AVCL,
- And do try to avoid crossing the insulation zone with pesky bits of metalwork!
Do you want to learn more about how to seal buildings professionally? Subscribe now for an advanced on-site training.
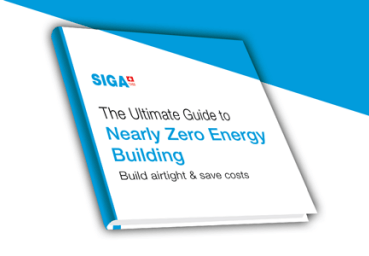
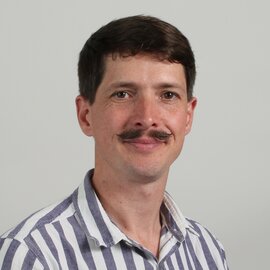
Bertie Dixon
Bertie has practised building services engineering and sustainability consulting in the UK for 15 years. He is a certified PassivHaus planner. He is on a mission to help you deliver a high-quality building, one that does what it says on the tin.