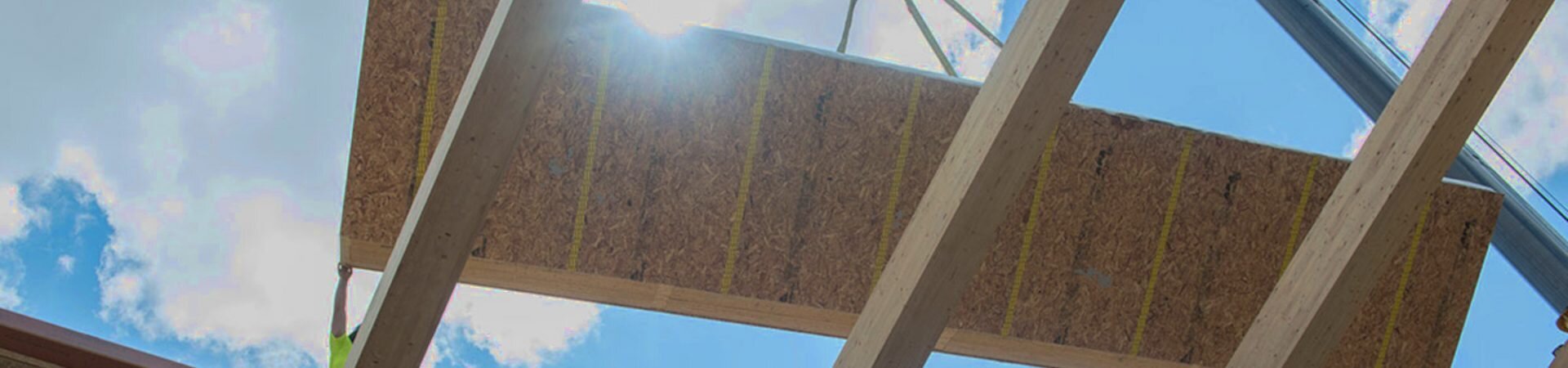
Brave New World: Challenges of Modular Construction
Modular and offsite construction are revolutionizing the building industry with speed and quality. However, challenges such as workforce training and market adoption remain before these methods can dominate.
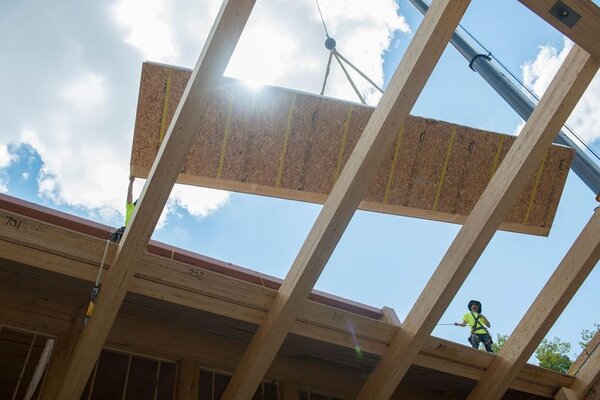
‘Modular’ and ‘offsite’ have both become buzzwords in the construction industry. These terms have come to symbolise a new, lean and hi-tech way of building. But what do these terms mean exactly? And what challenges do these modern methods of construction face if they are to become the future of how we build?
In this article we look at a practical example from the UK and Ireland. Nevertheless, in our opinion, these challenges are similar in other countries.
‘Prefabricated’ was once the most common term for construction that took place in a factory, rather than on a building site. But ‘prefab’ became something of a dirty word in the UK and Ireland, one that be came associated with poor-quality buildings. Today it’s much more common to hear companies talk about ‘offsite’ rather than ‘prefab’ construction.
‘Modular’ is a similar term. It specifically refers to buildings made in a factory from standardised components.
So how are these methods different from the way we typically build in the UK and Ireland? Here are some common differences.
Traditional construction
- Most construction work done on the building site
- Typical materials including concrete, brick, cement and plaster
- Airtightness and insulation carried out on site
Offsite construction
- Much more construction done in the factory
- Typical materials including timber (CLT, timber-frame) and light-gauge steel
- Building brought to site as modules or panels, and then assembled
- You can install airtightness products and insulation in the factory
The advantages of offsite
Most offsite systems are lightweight by their nature. This means they are easier to transport and lift into place on the building site. They are most often of timber construction, including traditional timber-framing or cross-laminated timber (CLT). Other materials such as light gauge steel are common too.
Offsite construction has grown rapidly in the past ten years, particularly because of the fast turnaround times it can deliver. It marks a big change from building with concrete and plaster on wet and windy building sites.
But building regulations are get tighter, and the demand for low carbon buildings is growing. So it is perhaps no surprise that offsite construction is becoming more popular with clients, architects, builders and developers. Its proponents argue that it has a number of key advantages:
- A warm, dry and well-lit environment for carrying out building work
- Attention to detail and quality control is easier indoors than out in the weather
- Much less time needed on site
- Easier to reduce and recycle construction waste in the factory
- Reduced health & safety risk in the factory (e.g. less time working at height on site)
Building in a dry & clean environment
“There’s definitely a drive towards offsite, everyone’s excited because it’s perceived as a new way of building,” says Nathan Beattie of Beattie Passive, which specialises in offsite passive house construction. “It can be done at scale and pace. And it takes away all the hardship of being on site and in the mud. You’re moving everything to a dry and clean environment. It’s a much more efficient and lean way of building.”
Nathan says that Beattie Passive completes “99 per cent” of its building work in the factory. This includes cladding, roofing, ventilation, plumbing and electrics. “There’s a box at the back of each module which you just plug into your electricity supply, water, and wastewater.”
Challenge in modular build 1: Bad memories of prefab
Despite the advantages, offsite construction still faces some challenges. In the UK and Ireland, the first is cultural. There is often a suspicion about different ways of doing things, and people still may be wary of anything that uses the term ‘prefabricated’.
A whole generation of British and Irish people will remember going to school in cold and poor quality prefab classrooms. These were often dropped into the yards of overflowing primary and secondary schools, with little thought for insulation, draught-proofing, or comfort.
Prefab today: Passive houses from the factory
But that’s a whole world away from how much of the industry does things now, Nathan Beattie says. “At Beattie Passive we’re delivering passive houses from factory, and they are a lot better than the vast majority of buildings built in the UK currently,” he says. “They’ve got 300 mm of continuous insulation, airtightness of 0.6 air changes per hour, mechanical ventilation with heat recovery, air source heat pumps, solar PV. It’s zero carbon passive housing, coming from a controlled environment.”
He adds:
«There’s a lot more education in the market now, and the passive house standard is definitely helping to drive the interest in modular too. Why would anyone want to live in a cold, mouldy house?»
Building offsite: think about quality, not speed
Architect Caitriona Kinghorn of Scottish offsite specialist MAKAR Homes agrees. MAKAR builds modular homes at its factory in Inverness, Scotland, using local Scottish timber. The company installs insulation, roofing, cladding, windows and doors in the factory. However, it carries out plumbing and electrics on site.
Kinghorn believes that there might be a need to change the way we talk about offsite construction now, to emphasise quality rather than speed.
«Perhaps there needs to be better understanding that offsite construction is best thought about in terms of better quality, rather than being cheaper or faster»
she says.
Challenge 2: Precise planning needed
Building offsite does, however, mean that projects require more precise scheduling. This requires something of a culture change on our building sites. The project team must be ready to erect modules, and make them weathertight, as soon as they arrive. Sub-contractors must work according to strict schedules. Clients will often have chosen an offsite system in order to drastically reduce the time needed on site.
One advantage of this approach is that it can cut construction waste because of the precision and control possible in the factory. Any leftover building material can be re-purporsed or recycled more easily there too.
And while the weather does not threaten offsite construction in the same way it does on-site building, there is still the challenge of protecting modules from the elements once they leave the factory gate.
Challenge 3: Protection from the weather
Precise planning is critical, so that when the modules arrive to site, the project team can erect and make them weathertight as soon as possible. The traditional solution for covering modules during transport was tarpaulin. But tarpaulin requires mechanical fixing, which is difficult and time consuming. It can also be a struggle to keep tarpaulin down, particularly during bad weather.
And while tarpaulin is waterproof, it is also impermeable to water vapour. This increases the risk of condensation when storing timber modules. Excess moisture can cause discolouration, swelling and warping of wood.
Because of the challenges with fixing and moisture, SIGA has developed a new membrane. Wetguard protects modular timber, CLT and steel frame elements during transport and once they arrive to the building site. It is both translucent and non-slip, making it easier to work with on site. It is also vapour permeable from the inside out, eliminating the risk of condensation causing damage to panels. And Wetguard attaches via an adhesive backing — there is no need for mechanical fixings.
“When modules are not protected for storage on site, this can lead to additional moisture damage. When moisture protective membranes are already installed in the factory, this will help us during windy conditions on site,” says Tony Cameron, site supervisor from offsite timber specialist Streif. “The key would be to only joint panels on site, which can easily be done with the 390mm tape of Wetguard.”
Challenge 4: Erecting modules in the wind
Perhaps the biggest challenge the weather poses is the wind. “As soon as there are high winds it becomes difficult to crane,” Nathan Beattie says. “You might set a delivery date but it can be changed by the weather forecast, so you have to be agile and adapt to certain situations.” Modules or panels must then be stored on site or nearby until the weather eases.
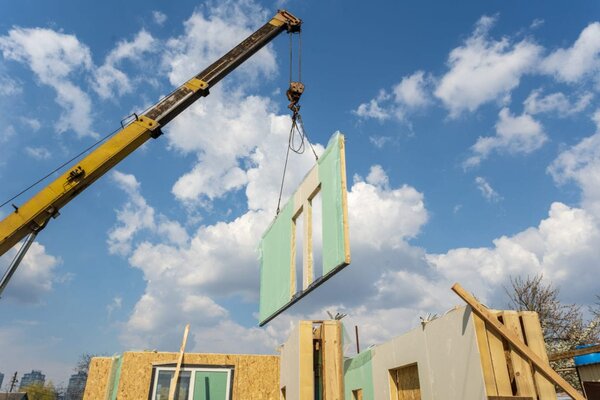
Challenge 5: Connecting modules on site
Of course, offsite construction does not mean there is no construction on site. Once modules are delivered, the challenge is to connect and finish them in a way that delivers an airtight, high performance building envelope.
In the case of Beattie Passive, a typical house might only need two of the company’s modules. Beattie Passive then connect these together on site.
“We make our modules as big as possible to minimise connections,” Nathan Beattie says. “The largest module we can do is twelve metres long by five metres wide. We construct our buildings as one whole unit in the factory, and then disconnect the modules. Once they’re on site, it’s simply a case of re-connecting them again. We leave a joint where the airtightness layer can be accessed and re-connected easily.”
MAKAR’s approach to connecting panels is similar, though it carries out more of its airtightness work on site. “Panels are connected via interlocking batten arrangements, which are screw fixed,” Caitriona Kinghorn says. “The panels are designed so that the screw fix areas are fully accessible during assembly. Airtightness is provided by the 18mm OSB board, which forms a continuous internal layer on floors, walls and roof, right up to window frames. These joints are taped once the house is weathertight, which means the airtightness procedure can be done in a warm and dry environment.” (Check out a time lapse of one of MAKAR’s recent builds, which featured SIGA Wigluv® tapes).
Challenge 6: Modular needs investment & upskilling
Perhaps the biggest challenge for the growing offsite industry in the UK and Ireland, though, is something much more ‘big picture’. “During my time at university I surveyed a number of Scotland-based builders for a university project about the up take in off-site construction,” Kinghorn says, “and the biggest challenge reported back was that setting up the specialist off-site facilities required huge investment.” The need to upskill construction workers for offsite construction is another major challenge.
Moving from traditional construction to offsite will take investment, innovation and up-skilling of our construction workforce. But climate change demands that we must change the way we build anyway. And the challenge of modular construction is one that, if we meet it, can ultimately pay off in the quality of homes and offices we live and work in, and in the size of our energy bills.
Read more about how SIGA Wetguard works and check out the latest case studies.
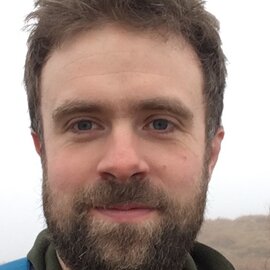
Lenny Antonelli
Lenny is a journalist who covers the environment and sustainability. He has been writing about the built environment for over a decade, and is deputy editor of the sustainable building magazine Passive House Plus.