The Ultimate Guide to A Safe Thermal Envelope
DOWNLOAD GUIDE HERE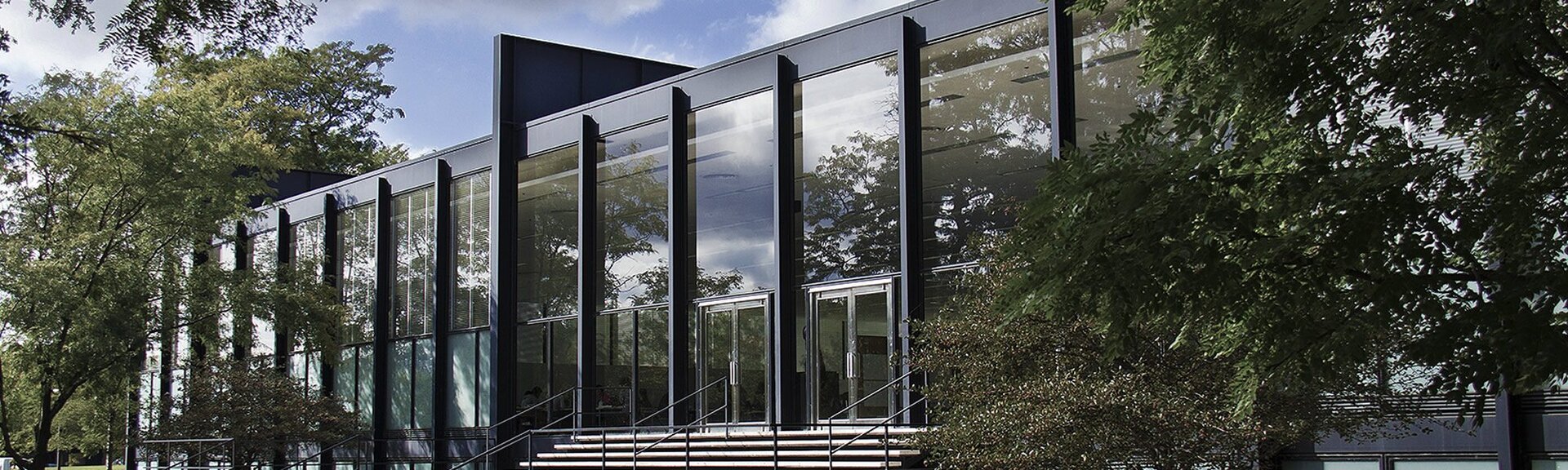
How to build a moisture-safe flat roof
Flat roofs can carry more risk of condensation and moisture damage. Here’s how, by using the right design and choice of products, you can achieve a safe and dry flat roof construction using the hybrid or ’compact’ roof principle.
We all love a stylish flat roof. Particularly since the birth of modernism in the 20th century, contemporary architecture has often been defined by flat roofs, clean lines, cubic shapes and generous amounts of glass.
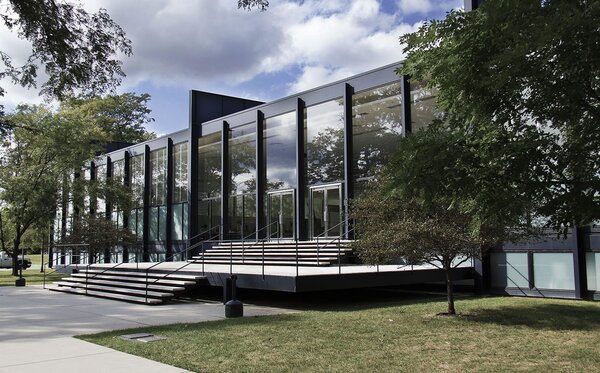
Crown Hall in Chicago by Mies van der Rohe (1956), home to the Illinois Institute of Technology‘s College of Architecture. Flat roofs, clean lines and large expanses of glass became a staple of modernist architecture during the 20th century (Photo CC-BY-SA 3.0) (Photo source here)
And in the past few decades this style has made its way from the offices and civic buildings of our city centres out into the suburbs, where flat-roofed, modernist-inspired extensions are now common on traditional suburban homes.
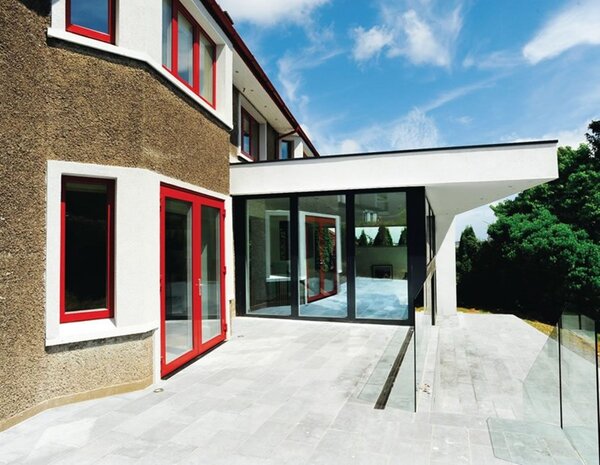
Modernism has also inspired many modern suburban extensions, such as this Enerphit retrofit project in Cork, Ireland by architect Andrew Shorten.
The moisture problem
But there’s just one problem: moisture.
In the rainy climate of the UK and Ireland, flat roofs must be covered with a barrier that is completely impermeable to water, otherwise rain that falls on the roof could seep into the structure below (EPDM, a type of rubber, is one of the most common materials used as a finish for flat roofs).
However, this turns one of the key principles of good roof design on its head. A typical pitched roof is designed to be more vapour open toward the outside of the construction, to allow any moisture in the roof structure to dry outward.
Rain hitting the pitched roof can run down the roof slates and fall to the ground, while underneath, any vapour in the structure can escape through the breather membrane into the ventilated space beneath the slates.
It’s not just rain, but vapour too
But because flat roofs must be finished with an impermeable material, there is a greater risk of moisture becoming trapped in the roof structure – potentially causing mould and rot – if the roof is not designed correctly.
Much of the moisture damage caused in flat roofs is not from rain getting in, but from water vapour within the building entering the roof structure, becoming trapped and condensing.
There are three typical types of flat roof construction: a warm roof, a cold roof, and a hybrid or “compact” roof. Each tries to solve this problem in a different way.
How a warm roof works
A warm roof is perhaps most common form of flat roof construction. In a warm roof, the insulation is installed over the roof deck. The roof deck is the key structural part of the roof, and in a flat roof it is often comprised of OSB or plywood.
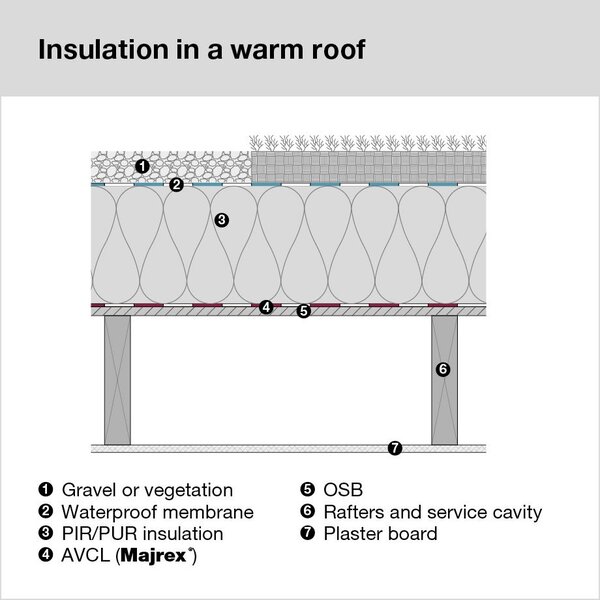
A typical warm roof construction.
Installing the insulation above the roof deck keeps the deck warm, meaning that even if there is an increase in relative humidity in the roof structure, it will be too warm for water vapour to condense to liquid. Water vapour in the air only turns to liquid below a certain temperature, known as the dew point.
The disadvantages of warm roofs
While this is a tried and trusted way to build a flat roof, it has a number of disadvantages. For a start, it can be more expensive, because of the need to install rigid insulation — rather than a cheaper material such as mineral wool — above the roof deck.
“Rigid insulation costs about four times as much as mineral wool, but the thermal performance is only twice as good,” says Stan Admiraal, SIGA’s Application Engineer for West Europe. “And because you’re putting all that insulation over the roof deck, it also means more brickwork and more materials, which increases the carbon footprint of the building too.”
How a cold roof works
In a cold roof, the insulation is installed under the roof deck. To prevent condensation on the cold deck, a ventilated gap is installed under the deck, through which outside air can move. The theory is that this lowers the relative humidity of the air adjacent to the deck and thus reduces the risk of condensation.
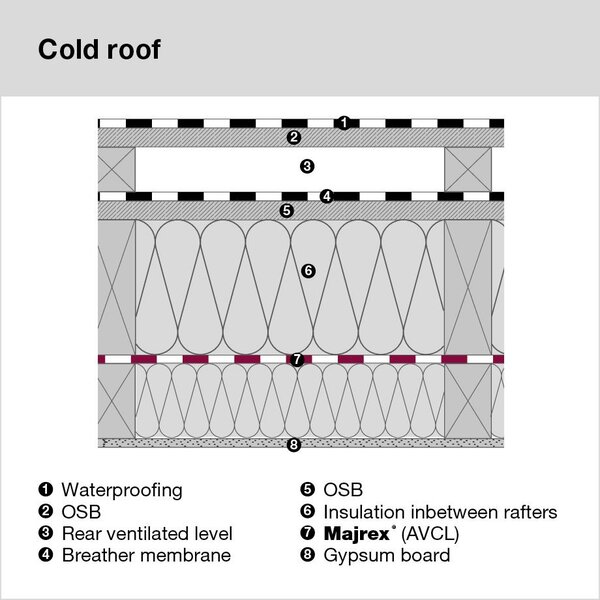
Typical cold roof construction with ventilated cavity under the roof deck.
“The problem is that this only works in theory,” Stan Admiraal says.
“In reality cold roofs carry significant condensation risk. The speed and direction of the wind varies all the time, and is not reliable enough to ensure consistent ventilation.”
It is common in cold roofs to install a slim layer of rigid insulation over the roof deck to help it dry out, especially if the roof does not receive sufficient sunlight. However, because this is separated from the rest of the insulation by the ventilated space, in practice it may not contribute to the thermal performance of the roof.
“In cold roofs, insulation above the ventilated roof deck is basically useless,” Admiraal says.
What is a hybrid or compact roof?
A hybrid or compact roof combines elements of both warm and cold roof construction. You install the insulation both directly above and directly below the roof deck, but there is no ventilated cavity.
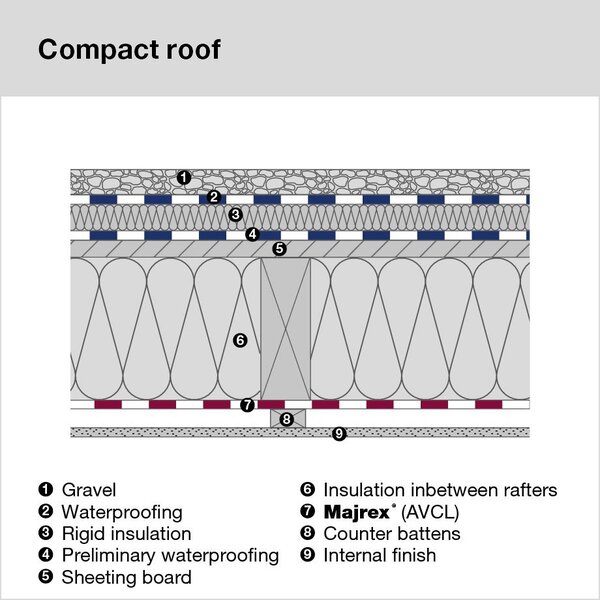
Typical hybrid or compact roof.
You put most of the insulation between the rafters under the roof deck, where it is suitable to use a lower cost mineral wool insulation. There is also no need for a thick construction above the deck.
However, you also install some rigid insulation directly above the roof deck in order to keep it warm and prevent condensation.
“A properly designed compact roof assembly is much safer than a cold roof construction, while being less bulky and more affordable to build than a typical warm roof,”
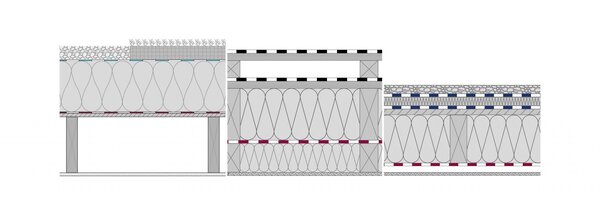
Comparing the depth of typical warm (left), cold (middle) and compact (right) roof constructions.
Is condensation a risk?
One concern raised with compact roofs is that the amount of insulation above the roof deck may not be sufficient to move the dew point to the outside of the build-up. And of course, there is also no ventilated space to introduce fresh air and remove moisture.
“If you build a compact roof with a normal polythene foil membrane, any moisture that gets into the structure will become trapped, greatly increasing the risk of condensation,” Admiraal says. “However, if you use a membrane like SIGA Majrex®200, which is vapour open in one direction, any moisture that gets into the roof structure can dry back out into the building.”
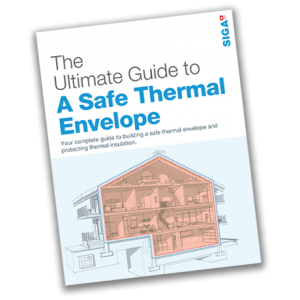
How Majrex®200 works
Majrex®200 features SIGA’s patented Hygrobrid® technology, which is much more vapour-open in one direction than the other. This means it can prevent moisture from entering the roof structure, while allowing any water vapour that does get it in to dry out.
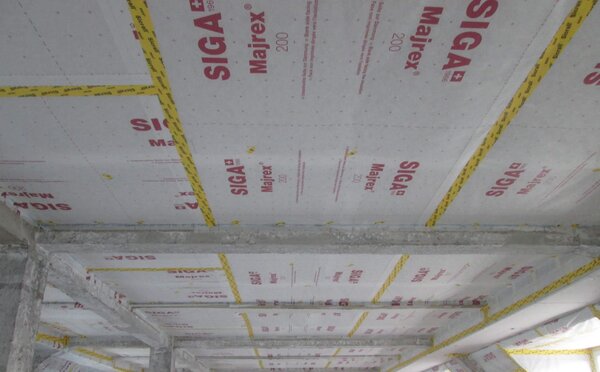
SIGA Majrex®200 was used in the retrofit of this historic building in Vienna.
Admiraal continues: “Most vapour-variable membranes open up in response to higher levels of humidity, but this is not always a good thing — for example during the wet trades stage of construction, excess moisture could migrate from the rooms into the roof structure. This is why it’s advantageous to have a one-way vapour control membrane.”
How to use a vapour control layer for a safe compact roof
“In a compact roof assembly featuring Majrex®200, and using a high quality rigid insulation with a lambda value of < 0.026 W/mK, you may only need as little as 60 mm of insulation above the roof deck to ensure a safe construction. We see this as a safe solution, and are happy to write a warranty for our product, and to perform condensation risk calculations for our customers.”
“All of our calculations even assume that the membrane is installed much more poorly than it should be in practice — this means that even if in a worst case scenario, you can rest assured knowing that your compact roof construction is safe.”
Compact roofs for retrofit?
Compact roofs are a good solution for renovating existing flat roofs too, Admiraal says.
“Of course you can retrofit by putting the insulation on top of the existing roof deck, and creating a warm roof, but you will have to increase the height of your building. You may need to extend your walls upwards, and even apply for planning permission.”
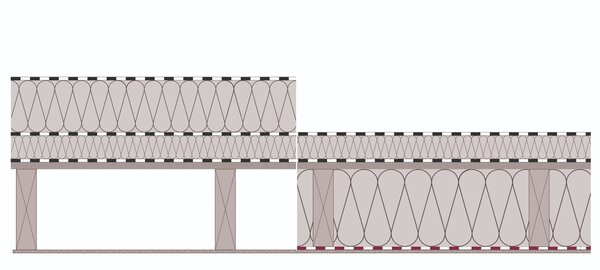
Retrofit of a flat roof using (left) the warm roof principle and (right) the compact roof principle.
“By retrofitting using the compact roof principle with a one-way vapour control layer, most of your insulation can go between the rafters in the form of mineral wool, and you can save a significant amount on the cost of insulation, labour and materials. You will also avoid the carbon emissions associated with all of that extra construction too.”
Peace of mind
Stan Admiraal concludes: “Overall, whether you are building a flat roof from scratch or retrofitting, a one-way vapour control membrane like SIGA Majrex® 200, along with quality design and construction, can help to ensure a moisture safe and affordable compact roof construction.”
Read more about how SIGA Majrex®200 works and check out the latest case studies.
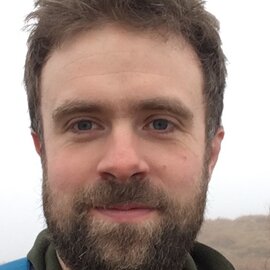
Lenny Antonelli
Lenny is a journalist who covers the environment and sustainability. He has been writing about the built environment for over a decade, and is deputy editor of the sustainable building magazine Passive House Plus.