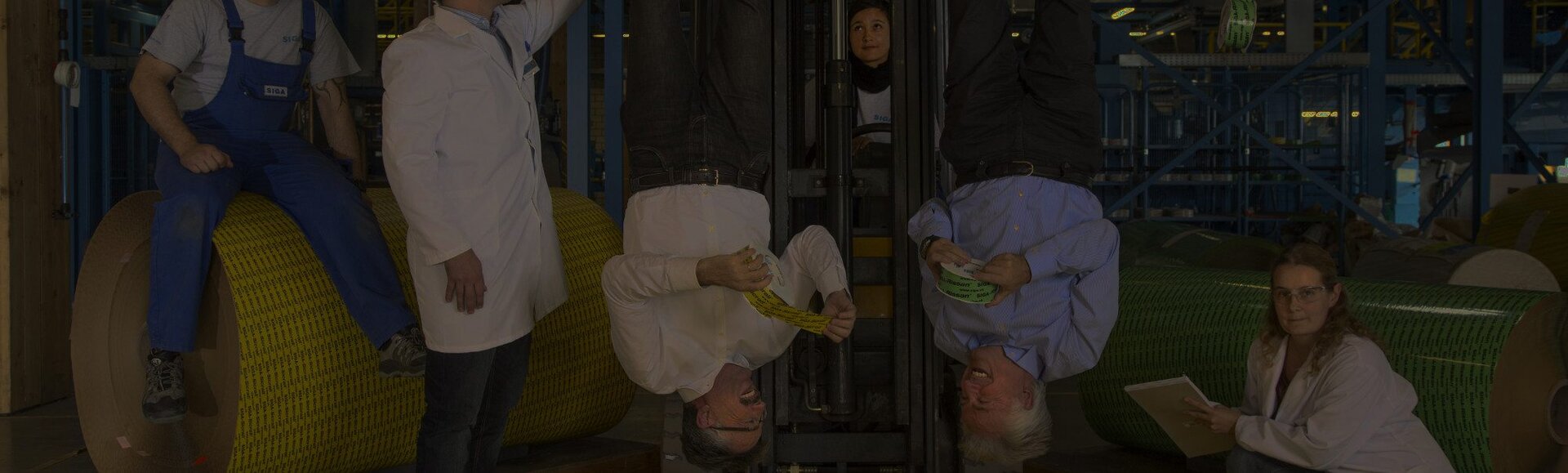
Meet the Experts at the SIGA Academy
Get hands-on with airtight building at the SIGA Academy. Learn from the experts, see how our products are made, and deepen your understanding of high-performance construction.
In this age of widespread digitisation and automation, the construction industry still resolutely depends on skilled people hand-assembling components. If you work in construction, as a designer or a builder, it is very important to get your hands onto the products you are specifying and using. I was lucky to be invited to the SIGA factory in the foothills of the Alps for their Airtightness Academy.
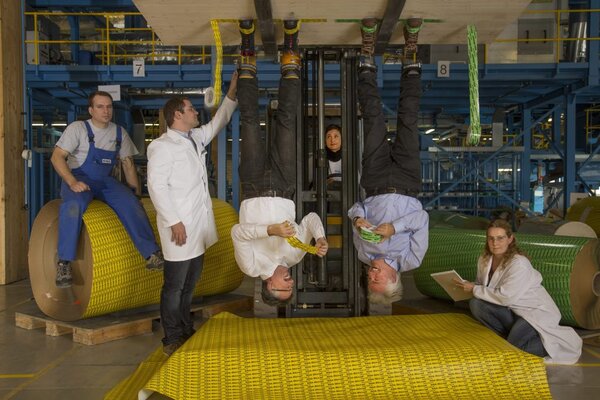
Marco & Reto Sieber – the owners of SIGA
I’m joined by ten other Brits;
- Contractors
- Architects
- Self-builders, and
- Consultants
Omar, a site manager, had used some of his holiday allowance to attend. He could see the value this training would add to his skill set.
The course content
Omar, and the 3,000 other people who attend each year, come here for an intense one-day training session. It starts with an essential grounding in the theory of moisture and air movement. Later in the day, we got to use many of the specialist tapes and membranes in the SIGA range.
Understanding the physics, and the build details
The presence of moisture is unavoidable in buildings, but it can be controlled through good practice. We learned about the causes of mould growth, the sources of moisture and how to manage this. I left with a good understanding of how to achieve moisture-safe construction.
The instructors covered the key physical principles for moisture and air movement, with hands-on examples of how to apply this to real-life construction. The course leaders are experienced technical reps from SIGA UK, so the course content is tailored to the UK/ROI markets.
The reps were careful to illustrate the building physics with practical experiments, so the concepts really hit home;
- Diffusion,
- Convection pressure,
- Application in the wet,
- Strength in the cold,
- Durability under movement, and many more.
For example, this trick demonstrated the strength of Majcoat® SOB at minus 25 °C.
Product demonstrations
SIGA develops each of its products in-house for a specific task. That’s why there are so many products available. Each has a number of clever, and often unique, features to make it a better job.
Once you are aware of the application range, you know which to turn to. It’s likely to be the best selection for the job.
For example, the adhesive layer on the pre-folded Corvum® tape is slightly wider than its paper backing. This is difficult to produce, but it means that when it is applied into a corner, the extra adhesive will completely fill the space – there’s no hole for air to pass.
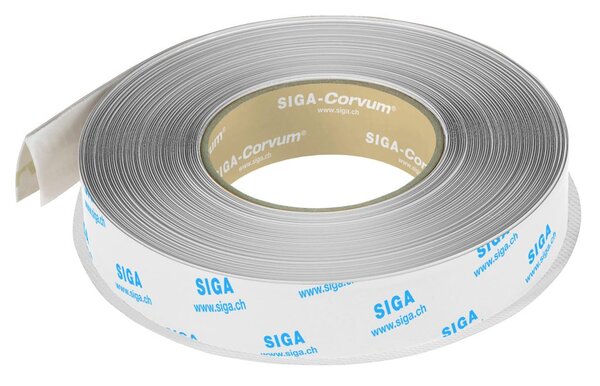
SIGA’s Corvum® fills a gap in the market
The SIGA crew deftly demonstrated the clever & unique features of the products in front of our eyes. Sometimes it feels like a magic show. Although unfortunately, I didn’t walk home with a balloon animal.
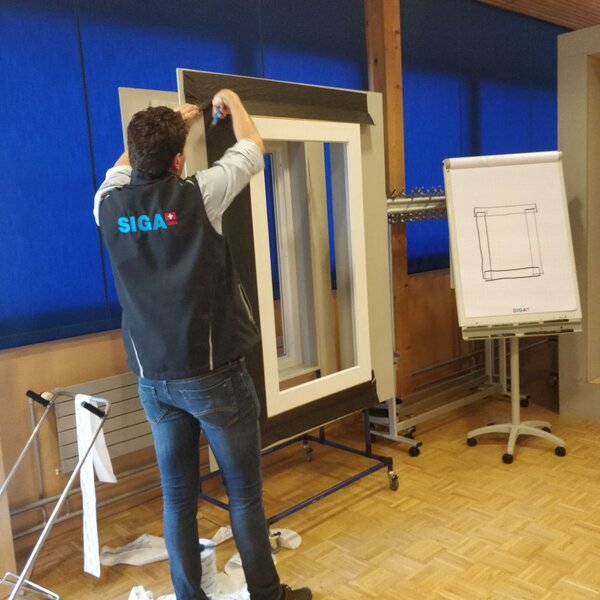
Window sealing & weathering demonstration with Fentrim® – faster, better & stronger than EDPM
A neat detail is the QR codes on the packaging of each tape. If you scan this it takes you straight to an online video demonstration of how to install the product.
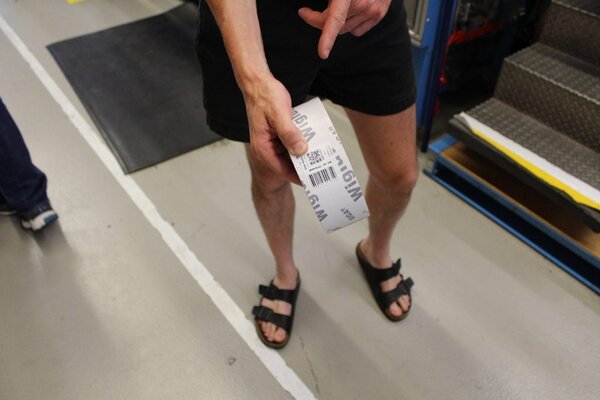
QR-code on SIGA’s adhesive tape Wigluv- links directly to the YouTube instruction
Using the product
Videos and demonstrations are all well & good, but they do not give you the same understanding as handling the product yourself. We worked in small groups to install membranes and tapes into a series of demonstration rooms.
It’s a little like being a tailor to an elephant- you need a certain amount of dexterity, and be good up a ladder. There is no right way to do a job (as long as it’s airtight), but you must think every move through before applying the product.
I have used competitor tapes and I found they were either not sticky enough, or way too sticky. I was impressed with the ease of install and tactility of the SIGA products.
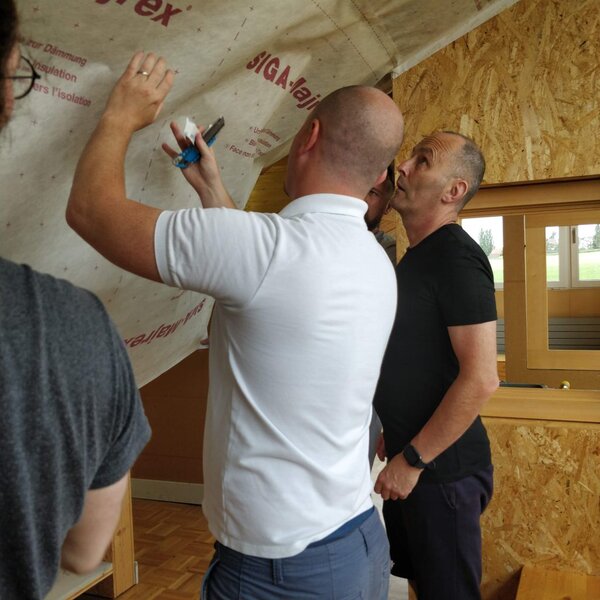
Hands-on practice in installing the membrane on a model in the SIGA Academy
Live Blower door test
We witnessed a mock-up airtightness test. The door is fitted with a calibrated fan, and the building is pressurised or depressurised to measure the leakiness of the building fabric.
Leaks may be apparent in a failed test result, but locating them can be tricky. We used thermographic cameras and smoke pens to identify where the air was escaping. This is when you really start understanding the air movement in the building.
The location
The SIGA factory could be straight out of a utopian future. Set in rolling wheat fields, with a backdrop of snowy mountains, staff cycle to work in a clean factory where innovation, improvement, and efficiency drive every decision.
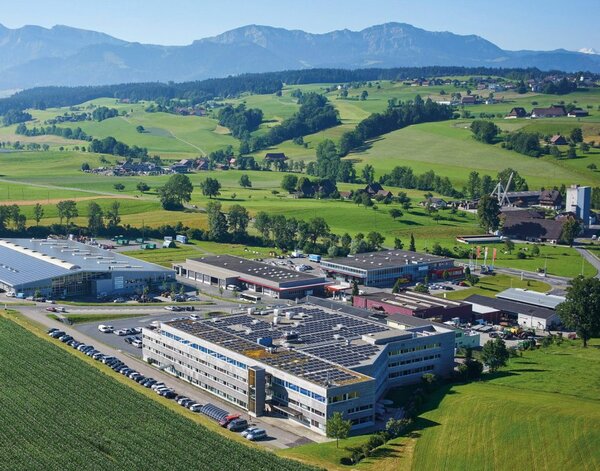
SIGA’s headquarter in Ruswil, Switzerland, near the Pilatus mountain chain
We stay next door, in SIGA’s guesthouse. This is an 18th-century building that SIGA have fully renovated. As is often the case in central Europe, the attitude towards high-quality construction shows through. Do you remember the VW Golf advert where they shut the door “if you listen carefully, it sounds just like a Golf”?
That’s how I feel in a building like this. It’s a manifestation of a culture of quality.
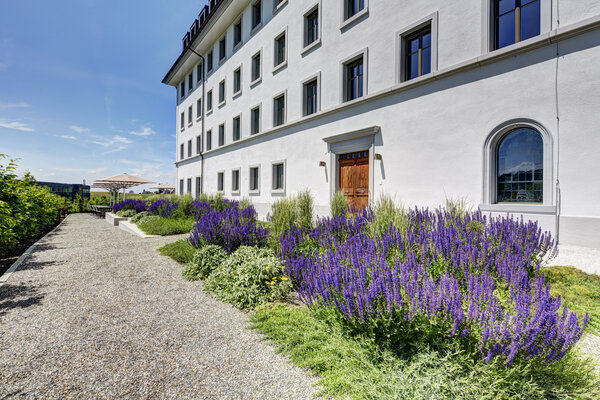
SIGA’s approach to Research & Development
But some qualities are not immediately apparent. For example, in as little as 4 years, adhesives in poor quality tape and mastics become brittle and powdery. To understand this type of behaviour you need to apply some science. We were shown around SIGA’s R&D department, which is where the science happens.
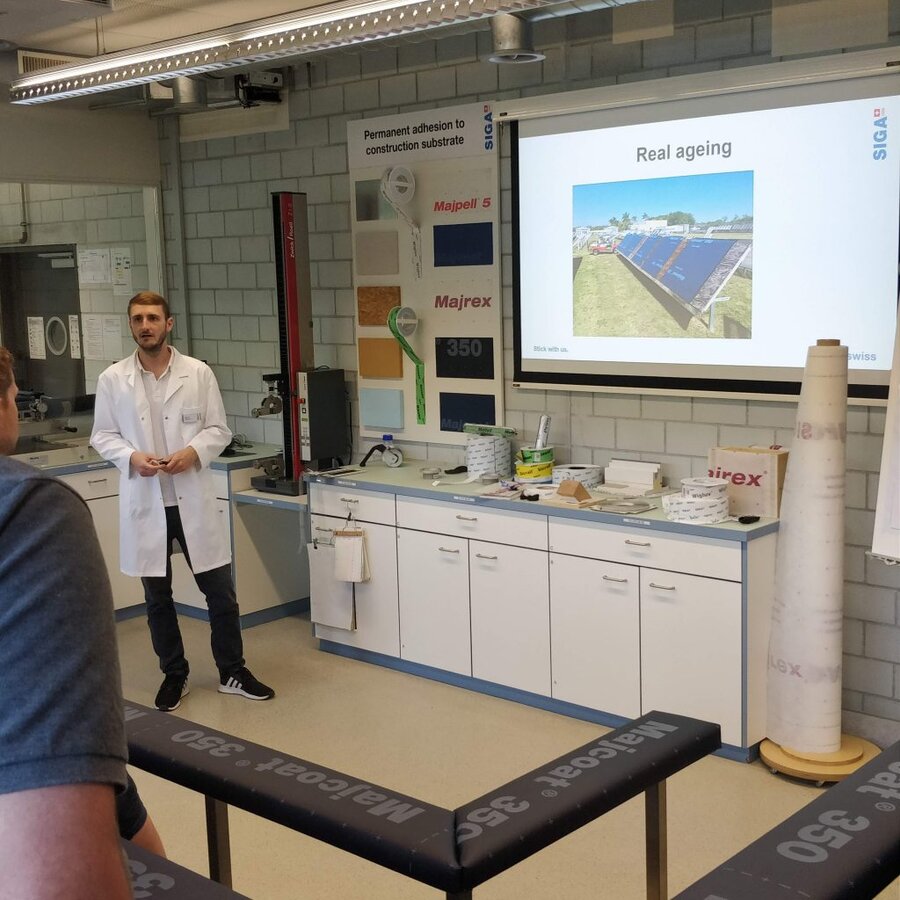
Over the last 53 years, since starting out making carpet tape, SIGA has come to focus purely on airtightness. They are the only such manufacturer with their own in-house R&D laboratory. It starts with identifying a customer need, and goes through the R&D process, ultimately to market. In the case of Majrex® it took 120 prototypes. SIGA currently holds more than 100 patents and patent applications spread across the globe.
Every 10th working day, for every employee, time is spent reflecting on how to improve processes. These guys are serious about doing a good job.
The factory floor: Where the adhesive tapes & membranes are produced
This attitude pervades throughout the company and onto the factory floor. SIGA has even product-developed in-house their own robotic machinery.
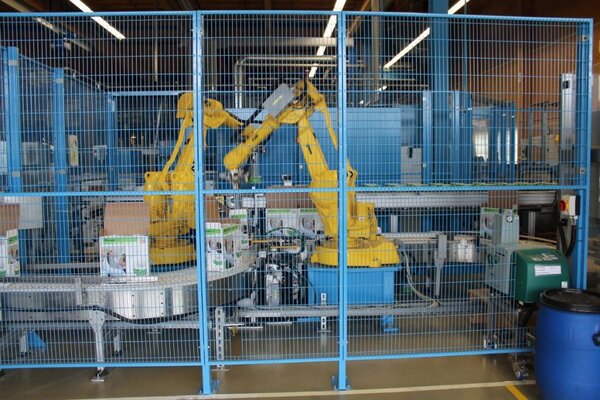
The SIGA factory – with robots developed in-house.
At the very start of my career, I worked in a copper cable factory in Manchester. The environment there could not be more different to here at SIGA. This space is bright, clean and very well organised. Lean manufacturing processes such as:
- Kaizen,
- Kanban,
- Six Sigma, and
- Just-In-Time Delivery
Are used to control quality and to ensure an efficient working environment. The modular timber construction and airy space reminds me of the forward-thinking Vitsoe factory in Warwickshire.
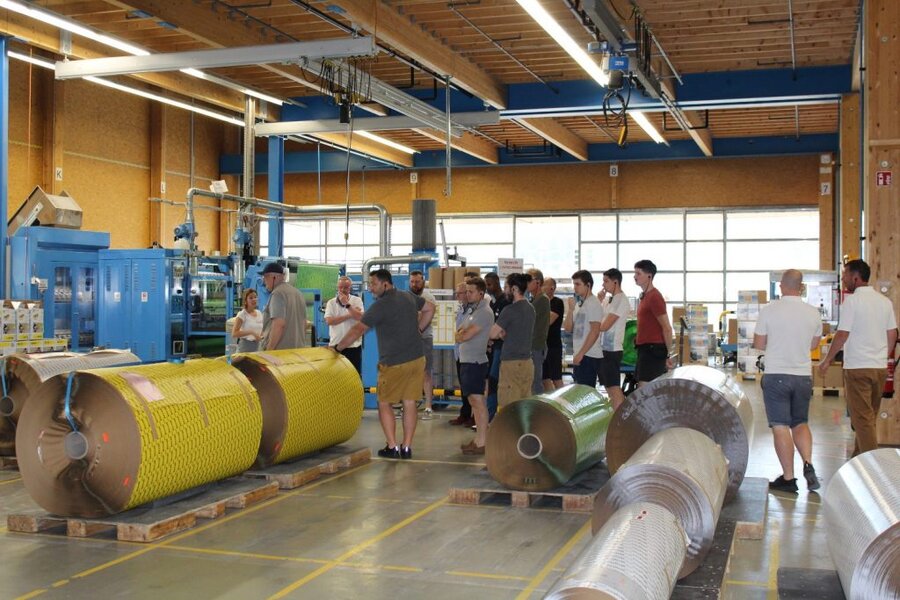
The day ended with a Q&A session which covered the big and little questions about airtightness that delegates were dying to know such as:
- Is it possible to be too airtight?
- How much does airtightness cost?
- What to do with curtain walling?
- How to detail flat roofs?
- etc
My take away; SIGA’s goal for zero energy loss buildings
SIGA has a vision for a world of zero energy loss buildings, with zero toxins, by 2066. It is not uncommon these days for companies to have a vision, or to sign up to sustainable declarations. What is quite uncommon is how focussed this particular company is on achieving its vision in practice. SIGA does this; not only by producing better products in an ethical way but also by sharing their knowledge with folk like you and me.
Although I have to say, a balloon dog to take home would have been a nice touch!
Day 2: Trip to the Swiss Mountains & Lake
After an intense session with a lot to take in, day two is time to relax- delegates are invited on an excursion that takes in a boat ride on Lake Lucerne, a mountaintop lunch and a cable car ride.
Does that sound like something for you? Contact us now for a non-binding inquiry!
Join the SIGA Academy
Sign up here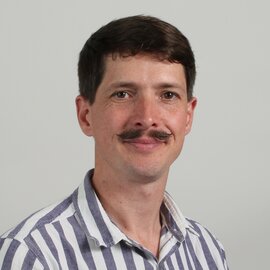
Bertie Dixon
Bertie has practised building services engineering and sustainability consulting in the UK for 15 years. He is a certified PassivHaus planner. He is on a mission to help you deliver a high-quality building, one that does what it says on the tin.