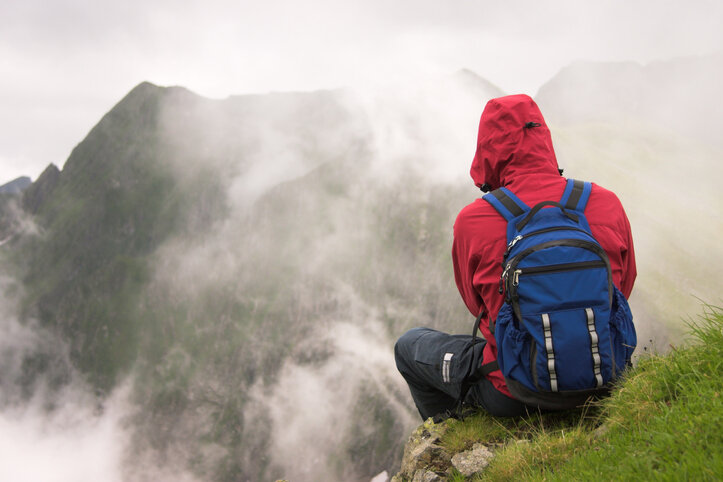
What does airtightness have in common with a Gore-Tex jacket?
An introduction to the main concepts for airtightness for UK & Irish contractors and builders.
Airtightness. Everyone speaks about airtightness, airtight building envelopes, vapour resistance or vapour control. But – what exactly is airtightness and why should UK and Irish builders have to deal with this topic?
This is the first of a series of articles that start with the basic principles of airtightness. Over the coming months, we will explore this topic widely.
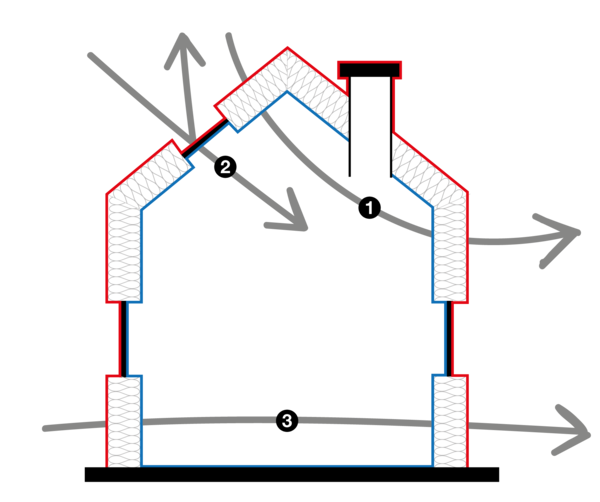
- Humidity moves in & out of the building & within the fabric driven by diffusion, capillary action or thermal gradients. It is also generated internally
- Solar heat may be reflected or may pass into the building. Internal heat is lost by conduction, convection and radiation.
- Mass air will flow through and within the building fabric. This is driven by thermal or wind pressure
Think of a building’s skin or envelope as a filter. As the image above shows, the envelope controls the passage of heat, light, air and moisture. If it is working well, it creates a comfortable & functional internal environment for just a little heating or cooling.
Achieving this doesn’t have to be difficult or expensive, but it does need planning. You may ask yourself; Why do I need to know this? The uncontrolled movement of air & moisture can cause all sorts of issues for the occupant, or for their builder!
- Discomfort from cold draughts & cold surfaces
- Respiratory health issues from mould growth within and on the surfaces
- Damage to the building structure from cold damp conditions (e.g. a 1mm gap in a build-up can allow almost 1 litre of moisture, per meter length, per day to enter a wall)
- Higher energy bills to heat or cool a poorly considered building (e.g. a 1mm gap can increase heat loss 400%)
- Failure to meet building codes
What is vapour control?
Even if it’s windy outside, it should be draught-free inside. By preventing the mass-flow of air through the building envelope, we prevent the replacement of warm air with cold. Depending on the precise conditions in the moment, any part of the envelope may be under negative or positive pressure. So, the whole envelope needs to be more or less completely sealed to the mass-flow of air. But, this does not mean it is a hermetic & sweaty bag. It must be airtight, yet moisture permeable.
Warm air in a building carries a lot of moisture. If externally it is cold, that is relatively dry. Just as a fluid flows from high pressure to low pressure, the ‘moisture gradient’ drives moisture from the warm & moist interior towards any cold surface it can find. As we know from our own experience (& from that scene in the Titanic film) when moist air hits a cold surface it condenses into liquid water. This causes extra heat loss and mould formation. So, how do we prevent this?
A well-designed building envelope will avoid cold surfaces not only by designing out thermal bridges but also by limiting the ability of vapour to diffuse outwards. This vapour control layer checks, or controls, the vapour movement driven by the moisture gradient. It is usual for the same layer to also be the air-tight layer that prevents mass air movement, too. The flow of air is totally blocked, but the vapour is simply checked or reduced.
What the building envelope has in common with a Gore-Tex jacket
Walkers are familiar with the onion skin principle: several layers of clothing worn on top of each other enable a well-dosed adjustment to changing weather conditions and the body’s own heat production.
The building envelope is rather like a Gore-Tex jacket, that stops the wind but allows your perspiration to diffuse through.
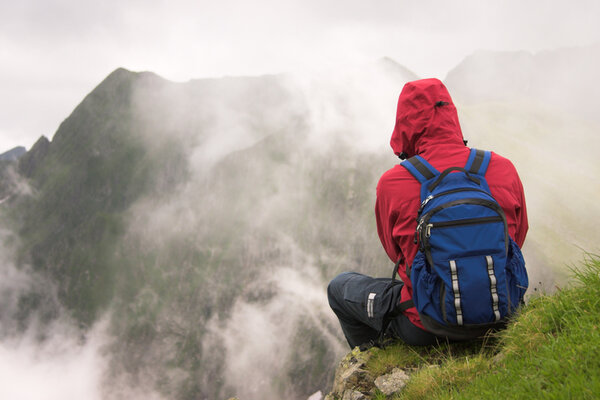
Gore-Tex jackets – they are waterproof & breathable
So, some moisture gets past the vapour control layer. The design of the layers must be such that any such “interstitial” moisture can easily diffuse out without meeting an impermeable barrier. Hence, the vapour check layer is usually selected to be the most vapour resistant layer, with subsequent outer layers to be less resistant.
*Impermeable ‘warm’ roofs are an exception to this principle, that require special attention to limit air flow to the cold external surface & allow drying in summer. More on this in a later blog.
We have described an air-tight yet breathable construction which will allow safe moisture movement in both directions, as will happen over the seasons of many years. For example, during the summer, the outside is now warm and the inside cooler. Hence the moisture gradient is reversed. Warm moist air will condense if it comes into contact with a cool impermeable surface. If this happens, it can cause issues, especially in air-conditioned buildings in humid climates. A high quality assembly- that prevents mass air movement including ‘thermal bypass’- is the best way of preventing this from occurring. ‘Intelligent’ membranes will change their properties to adapt to this situation.
The main types of vapour control and airtightness control
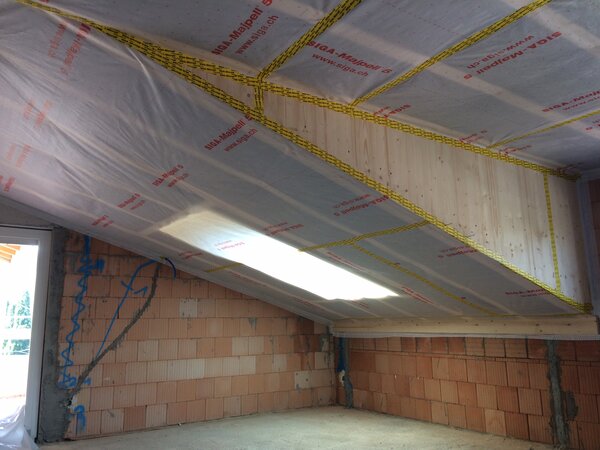
Membranes; flexible sheet on a roll
- Slim: less than 5mm thick
- Adaptable to any shape, e.g. to old/complicated buildings
- Can have dynamic “intelligent properties”
- Can easily be pierced – requires protection
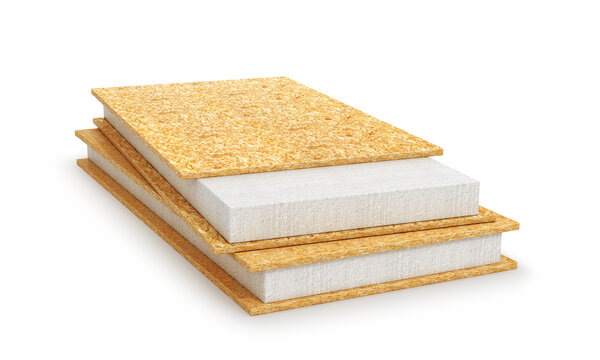
Boards; such as OSB or sheathing board
- Thickest; around 25mm
- More robust
- Quick to install, but heavy to handle
- Flat – difficult to coordinate with curves or existing buildings
- Can hide problems once installed
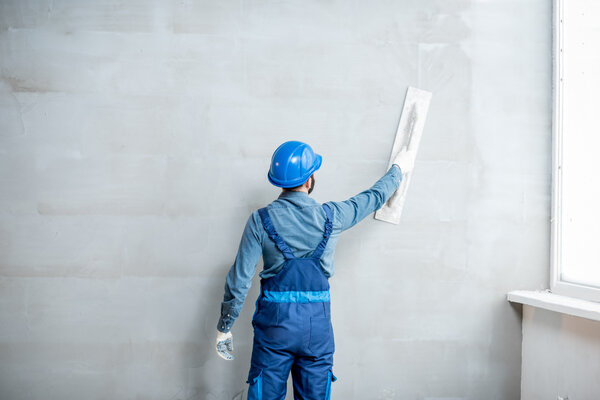
Wet trade; such as plaster or liquid plastic
- 10-15mm
- Fewer tapes & seals
- Most robust
- Adaptable to any shape e.g. to old/complicated buildings
- It is an extra wet trade; more time, mess & moisture
- Liquid plastic is not as breathable- may only suitable for small areas
Getting it right
Selecting the right vapour control & airtight layer is important but it is only one part of the journey. The pursuit of very low leakage is a particularly large rabbit hole; it is a whole specialism in itself. We’d recommend seeking professional guidance early on, to give yourself the best chance of success.
As we said, it doesn’t have to be difficult, but it does need careful thought. We will go into more depth in later articles.
I'm interested in attending a SIGA workshop
Book your SIGA workshopIn the meantime, here is a summary of the main tasks:
- Work out how to achieve a continuous, complete and gap-free airtight & vapour control layer. This requires the resolution of all the junctions between all the building elements, structure and services. Draw out key sections & resolve each junction. Build a mock-up of any tricky details. Use the mock-up to induct trades.
- Protect the vapour barrier once it is built until handover; not only through physical protection but also by training of operatives.
- Consider running fault-finding air pressure tests at gateways during construction, in addition to the final test at completion. These may be coupled with smoke-tests and thermographic imaging in order to seek out leaks.
Finally, now that you have “built it tight”, don’t forget to “ventilate right”. And that is a whole other discussion.
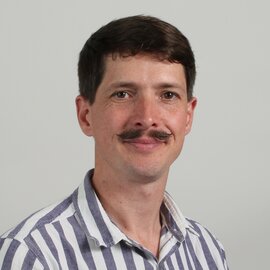
Bertie Dixon
Bertie has practised building services engineering and sustainability consulting in the UK for 15 years. He is a certified PassivHaus planner. He is on a mission to help you deliver a high-quality building, one that does what it says on the tin.