
Find your way through the labyrinth of UK building regulations
Learn how to control air movement for condensation control in the UK.
This is Part 2 covering UK regulations risk of condensation & weathering regulation.
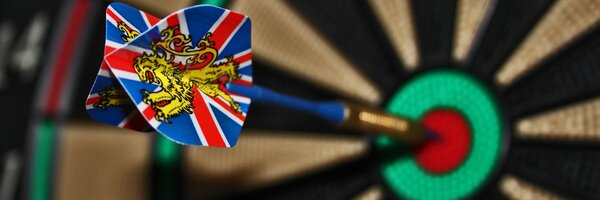
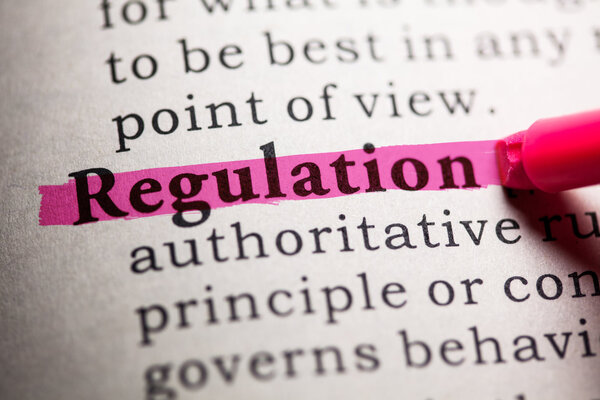
If you are in Ireland, check out these articles – they cover important building regulations in your country.
Read more about Irish building regulationsWe are experienced enough to know that we can occasionally make mistakes! This article is advisory only; we do not claim completeness, accuracy or liability. Please highlight any errors or additions by commenting.
Control of air movement for condensation control
For our sins, we live on a damp island in the temperate North Sea. Our homes and buildings are uncommonly small, and they are often poorly built and ventilated. All of this points towards a risk of condensation.
Condensation in building fabric is a complex problem. It can occur completely hidden from view, yet be causing severe damage to building fabric or occupant health. Working to avoid damp is a major part of a builder’s responsibilities.
Approved Document C – Site preparation and resistance to contaminates and moisture 2013
This is the relevant approved document for condensation control. Paragraph 0.2 requires that the building envelope be constructed to protect the building and occupants against the effects of moisture from
- Precipitation
- Interstitial & surface condensation.
- Ground water
- Leakage from wet services
Preventing rain from penetrating the building envelope is of course essential. Paragraphs 5.8-5.28 describe the external wall protection. The required construction depends on the weather severity rating of site location. Please refer to diagram 12 & table 4.
Check out diagram 12 UK zones for exposure to driving rain as well!
The building envelope works hard. It must do at least the following:
- Weather proofing
- Thermally insulating; also limit thermal bridging and thermal bypass
- Reasonably Air tight
- Limit vapour movement to control condensation
Below we have interpreted Diagram 11 from Part C to show which product is suitable for each application in walls and roofs. We’ve interpreted them to identify which SIGA product is best suited as the vapour control & airtight layer (in red dashed) and wind/weatherproof membrane (blue dashed line).
The subsequent paragraphs go into some more detail: e.g. 5.23 states that if cladding is impervious it must have a vented cavity behind. Flat roofs without rear ventilation requires calculation by dynamic methods. SIGA can help you with this, to consider convection and moisture capacity. If the modelling shows its low risk, we can validate the use of Majrex® for your situation.
5.27 states that timber framed buildings certainly require a cavity. Paragraph 5.29 states that the join between windows and walls must be impervious- SIGA Fentrim® fills this gap.
Paragraph 5.34 requires that walls do not create interstitial or surface condensation under normal circumstances. There are similar generic statements for floors and roofs.
So document C sets the broad principles, but is quite light on applicable design guidance. Have a look at BS 5250 for more on that.
BS 5250 Code of practice for the control of condensation in buildings (2002)
Approved document C refers to this standard. It contains a wealth of useful information for the designer and builder.
Paragraph 4.5.1 of this BS gives us the main takeaway principle:
“Water vapour is transferred through materials by diffusion, but much more significantly, water vapour transfer occurs as a result of air movement. Therefore, when designing to avoid the risk of damaging condensation, air filtration into and air leakage through the construction are the most important mechanisms to be considered.”
I.e. make sure you have a vapour control layer in place that is suitable, high quality & unbroken. We covered the main types of vapour control layer in this blog post.
The quote above also shows why ‘breathable’ yet air-tight building materials are good practice. They allow moisture transfer by diffusion, not by mass-air movement. So, they do not significantly increase the risk of condensation. In fact, they will reduce the risk, as the breathable nature will allow any trapped moisture to make its way out of the fabric. Conversely, leaky yet vapour impermeable materials, such as rigid/foiled insulation, will create problems in time.
Annex M is a useful short site work guide for builders.
Annex F, G & H contain a wealth of typical build-ups of floors, walls and roofs. This is a very useful reference guide for designers & builders. It should be referred to in assessing condensation risk.
Finally, if you are building a high humidity building such as a pool, you are certainly going to need some specialist advice. (And if you do a really good job of vapour control you can up the design internal humidity levels. This has consequent benefits for running cost and efficiency. See how the Passivhaus fraternity are doing it.
NHBC Standards
Many new UK homes are warrantied under the National House Building Council’s insurance scheme. Other scheme do exist and will have their own requirements, but NHBC is the most common. If your scheme is NHBC warrantied, the NHBC requires compliance with its standards guidance & this covers airtightness.
We will not attempt a full summary of the standard here, but we give you occasional advice on how to limit air infiltration.
There are detailed, and sometimes dubious from a thermal perspective, requirements for vapour control layers which is developed in each of these chapters:
- Chapter 6.2 ‘External timber framed walls’
- Chapter 7.1 ‘Flat roofs, porches and balconies’
- Chapter 7.2 ‘Pitched roofs’.
Protection during construction
The sooner that a site can be made weather-tight the better, as this allows internal works to commence sooner. Many sites rely on the facade membrane & roof underlay to act as a temporary weather-proofing line which can allow the interior to proceed sooner that it otherwise might have. NB The product must be protected from UV within a certain period- check the datasheet.
The construction stage, and the first two years, are a critical period where the amount of water in the building is far in excess of the normal. Wet trades such as concrete, plaster, screed, and poor weather during construction all add to the moisture load that the building must deal with. So, even if the design is correct for the normal case, some extra allowance must be made in the design of vapour control & release in the fabric. This must be done to take account of the higher risk of condensation during this period. If you have many wet trades on site & soft insulation, the risk is very high. We propose Majrex® is used to control the risk.
Conclusion
We have given a brief summary of airtightness for condensation and weathering regulation for the UK. You can find more guidance on airtightness control for efficiency & comfort in this blog post.
The principle is to prevent mass airflow of warm and wet air to cold surfaces. Cold surfaces are unavoidable, so the requirement must be to limit the air flow. You can do this with a continuous air & vapour control layer (AVCL). In this way an airtight building is likely to have a very low interstitial moisture risk, too.
This AVCL layer can be ‘breathable’, ie vapour-open, as this does not significantly increase condensation risk. In fact, it reduces it as any trapped moisture can eventually escape.
If the design follows the principles of the standard arrangements in BS 5250 appendix F, G or H, it is unlikely to present a risk.
If you step outside this guidance, you may need some specialist products, advice and analysis. SIGA is on hand to help you with this.
Get in touch with SIGAOther useful guidance
BRE IP 5/06 condensation in Roofs
Further guidance on avoiding condensation in warm & cold roofs
BS EN ISO 13788 and BRE Information Paper IP 1/06 [9]. BS EN ISO 10211
Method for calculating thermal bridges and surface temps to demonstrate risk of condensation.
What’s missing?
If you feel we’ve missed a critical piece of guidance, let us know in the comments.
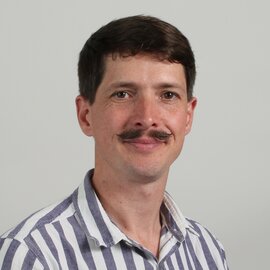
Bertie Dixon
Bertie has practised building services engineering and sustainability consulting in the UK for 15 years. He is a certified PassivHaus planner. He is on a mission to help you deliver a high-quality building, one that does what it says on the tin.