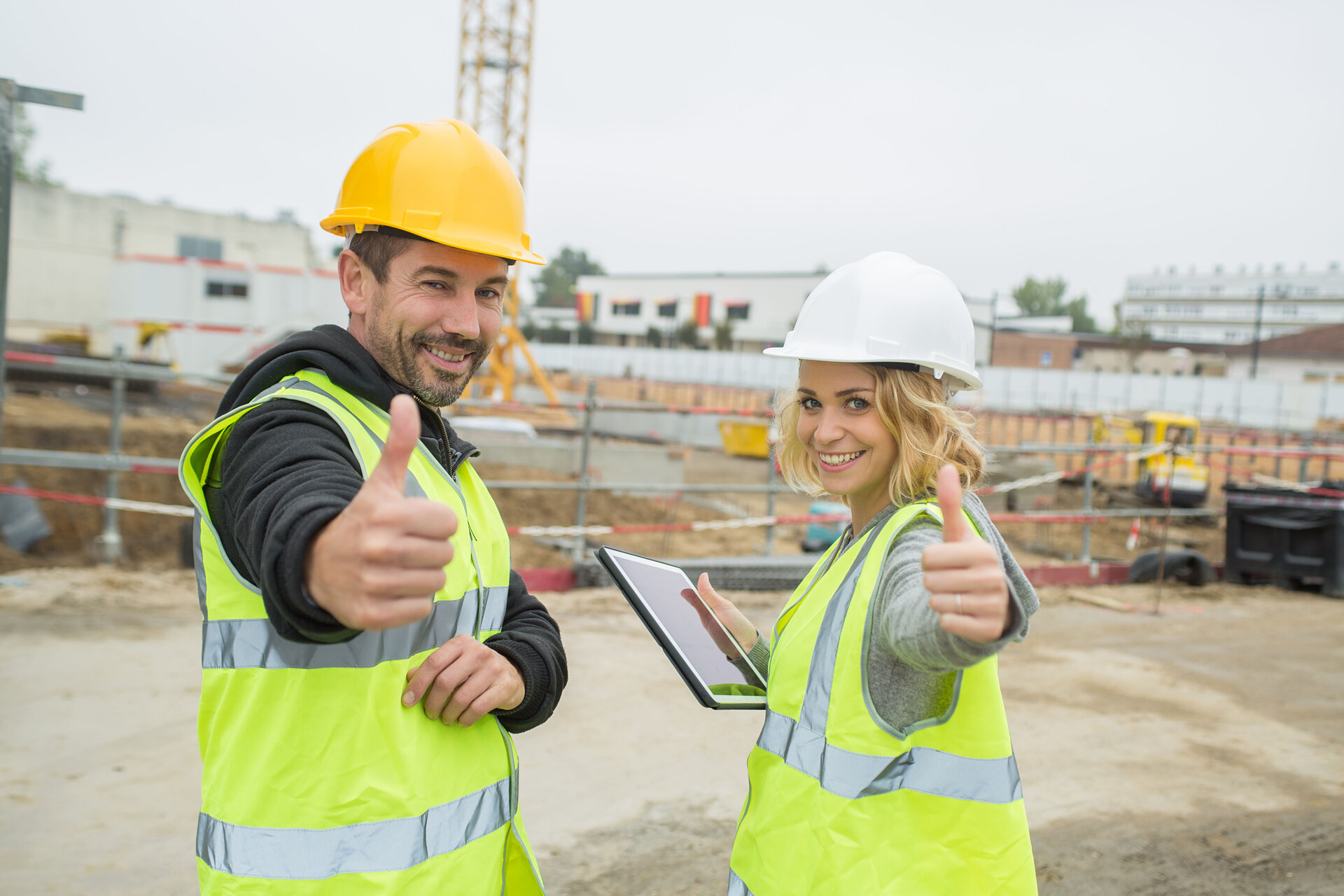
Getting the best results without extra cost – how is it done?
In Part 1, experts reveal how quality construction can meet high performance standards while staying within a standard build budget. Discover their design and construction strategies for cost-effective results.
We saw in Part 1 of this feature that high quality buildings are being built successfully, on constrained budgets, in many places. What can we learn from these projects?
We start in the design office. This is where the most expensive decisions – and sometimes, the most expensive mistakes - are made.
The cost of a project is determined VERY early
Some of the very earliest decisions about a building – right at the sketch-on-a-napkin stage – can be the most crucial for final cost. These early choices determine whether a building is going to be straightforward to construct, or whether it is going to be difficult and expensive, involve high materials costs, and hard to get right on site.
As engineer Nick Grant of consultancy Elemental Solutions puts it: “Most costs are incurred at a very early stage in design – but this is the stage where the largest savings can be made for least effort. (see diagram)
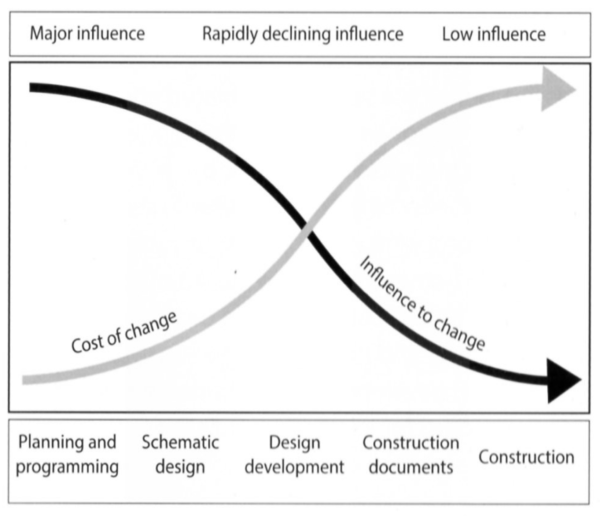
Engineer Nick Grant often shares this diagram illustrating the way that early decisions have a major impact on project cost – the later in the project you leave it, the harder and more expensive it is to put things right. (Graph by Mark Siddall, LEAP, inspired by Boyd Paulson, 1976
Tobias Unger is an energy engineer in the Bavarian State Environment Office. He has carried out research and developed guidance on cost-effective high-quality construction for the state government of Bavaria. Unger agrees the early stages are critical to final costs.
Exchange information early
Unger strongly recommends the team gets together early. This allows potentially expensive mistakes to be identified while there is still the chance to put things right.
“A kick-off meeting enables the various players (architect, energy planner, structural engineer, electrician ...) to exchange information. Problems in individual areas can be solved quickly.”
He recommends these “parallel working” team meetings carry on throughout the project. “The sooner a problem is shared, the easier (and cheaper) it will be to put right,” he says.
Tobias Unger gives an example of a problem that is straightforward to resolve at the start of a project, but very expensive to put right later on: “If, for example, an early-stage simulation by an energy planner shows heat protection in summer is too poor, the architect can reduce the building's glass area.
“If no adjustment were made during the design process, alternative countermeasures would have to be taken, such as additional shading or active cooling.” Compared to a simple change early on, this would be an expensive way to solve a problem that could have been avoided in the first place.
Doesn’t this extra work up front cost more?
No, because those early conversations are where the money saving changes can be made, Unger says. “Integral planning with early involvement of all stakeholders does not result in additional costs at the end; they will, rather, be avoided”.
Complicated buildings are expensive!
As Nick Grant points out, basic geometry means that any deviation from a rectangular plan will increase construction costs per m2 of useful floor area.
“Increasing the form factor means there is more wall or roof to build for the same amount of floor space - this is basic geometry!” So costs go up immediately, as more materials have to be bought. Features like overhangs also add structural costs, and sometimes more expense on top to avoid thermal bridging.
If working to an energy use target, a larger area means the thermal performance of the entire envelope has to increase. This is to make up for the fact that there is more envelope area through which heat is being lost. So, more building, and more expensive per m2 of envelope on top.
Complication adds uncertainty
Contractors don’t like uncertainty. And the more complex-looking the building, the less certain contractors can be about costs on site. So they will naturally give a higher price, to cover the unknowns. Progressing the design to a more detailed stage can offer contractors more certainty, and thus open the way to better costs. But even better to have a more buildable design in the first place.
As Nick Grant and his designer colleague Charles Grylls of Dempsey Decourcey Architects know, “an experienced builder will have a deep learned intuition for where hidden structural costs or savings lie.”
“They will spot costs such as additional steel work and will recognise the kind of ‘tricky details’ from previous project where unexpected costs were incurred.
When presented with a completed design, these kinds of details “typically result in a deep sucking in of breath and the phrase ‘not cheap’.”
Sadly, as Grant and Grylls point out, “this contractor experience is rarely present in the design team until it is too late to design out the problem”. Instead, the builder’s input to cost control will be limited to suggesting cheaper, and probably inferior, materials and components” – a hugely wasted opportunity.
Keep hold of your learning!
Nick Grant and Charles Grylls are long-term collaborators with builder Mike Whitfield, and work in an integrated team of architect, energy consultant, structural engineer, services engineer and builder.
The team works on repeat projects, so that lessons from past builds feed back into design. This approach enables an impressive level of cost control, with bespoke Passivhaus builds competing on cost/m2 with standard builds.
The message from all the researchers is ‘keep hold of your learning, and don’t re-invent the wheel’. Think how much time and money you save in the office and on site if you use a detail that has been tried and tested in an earlier project. It’s already drawn, it’s already calculated – and it’s already been successfully built.
Don’t be afraid of standardising
Research by buildings and energy expert Professor Axel Bretzke, presented at the International Passivhaus Conference, made it clear that designing and building with quality assurance and standardised details results in cheaper solutions and faster builds. By making everyone’s job quicker and simpler, quality can be maintained. By contrast, individually designed buildings with every detail designed afresh “means individual solutions with a lot of mistakes and extra cost”, the converence heard.
This does not mean standardising entire buildings – individual buildings should still be tailored to the site and the client’s requirements. But it does mean you can make big savings by using standard details. Part of the Bavarian government drive to increase quality and cut costs in their construction sector, involved the publication of standardised details, for insulated foundations and the installation of doors and windows for example.
Share the learning, share the success
The collaborative learning generated by an established team can be invaluable when working with less experienced colleagues. For example, Nick Grant and Charles Grylls took their optimised details on to a project with builders inexperienced in delivering high levels of airtightness. But, they said, they needed only a few drawings to detail all the air and weathertight junctions. “We made one visit to demonstrate taping, and the first blower door result was 0.09 m/h.” Simplicity here was the absolutely the key to quality at no extra cost.
Save money by getting it right first time
It is the design team’s job to keep on top of capital costs and ensure it is straightforward for the construction team to deliver a quality build. But things can still go wrong on site, if roles and priorities are not clear, and if systems are not set up to solve issues - before they become faults.
Help teams understand each others’ work
Once again, experience shows that collaboration is key. When looking for a quality result, for example, in terms of air-tightness, continuity of insulation, excellent finishes – all the different parts of the team need to understand what their site colleagues need. Carpenters need to know where insulation is going to be installed, so they don’t block access by mistake. Services teams and plasterers need a clear indication of the airtightness line, so holes aren’t cut in membranes then hidden before they are spotted. The team laying a screed need to be aware that the tiniest lumps and bumps will be found out by brittle porcelain tiles. And so on.
This is not always easy with an ever-changing cast of sub-contractors. But if the right culture and ethos is embedded on a site, things go a lot better.
Alex Honey of consultancy Enhabit describes his experience in a large-scale retrofit project for Clarion Housing. Different trades and subcontractors were coming together regularly to check through the plans and solve any issues. “This has been a very rewarding project because there is a great spirit of collaboration and openness. The site manager from the main contractor has been able to bring everyone together, and ensure they all “got” what we are trying to achieve.”
Site crew can lead the way to savings
As with the initial design, two-way communication on site leads to effective, affordable solutions. At the Clarion project, site crew were empowered to generate solutions that would have been hard to devise on paper. For example, the hands-on crew perfected a way to quickly install the supporting frame for window installation, and give a sharp, accurate finish that could readily be made airtight.
Successful teams have found onsite training to be a good investment. Many component suppliers offer toolbox talks – and some set out quality assurance procedures - because they want their products to perform well. Independent site training is also available. Half a day of hands-on training is a lot cheaper than finding components are not fastened, sealed, or aligned as they should have been - when it’s too late to sort it out.
Rewards for everyone
At the end of the day, no-one sets out to do a bad job when they go to work. The commercial rewards from doing a good job are self-evident: as Axel Bretzke’s conference paper put it: companies that follow clear standards for design and construction “will be able to assert themselves in the market”.
But the rewards are arguably deeper. As New York developer Alex Bernstein told the North American Passive House Association conference in 2020 : “It’s all our contractors yearn to produce – a building they can be proud of. They won’t go back to a different way of building. This transforms people’s lives.”
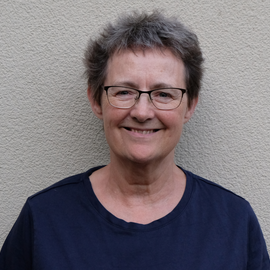
Kate de Selincourt
Kate is a writer and researcher specialising in sustainable and healthy building and retrofit.