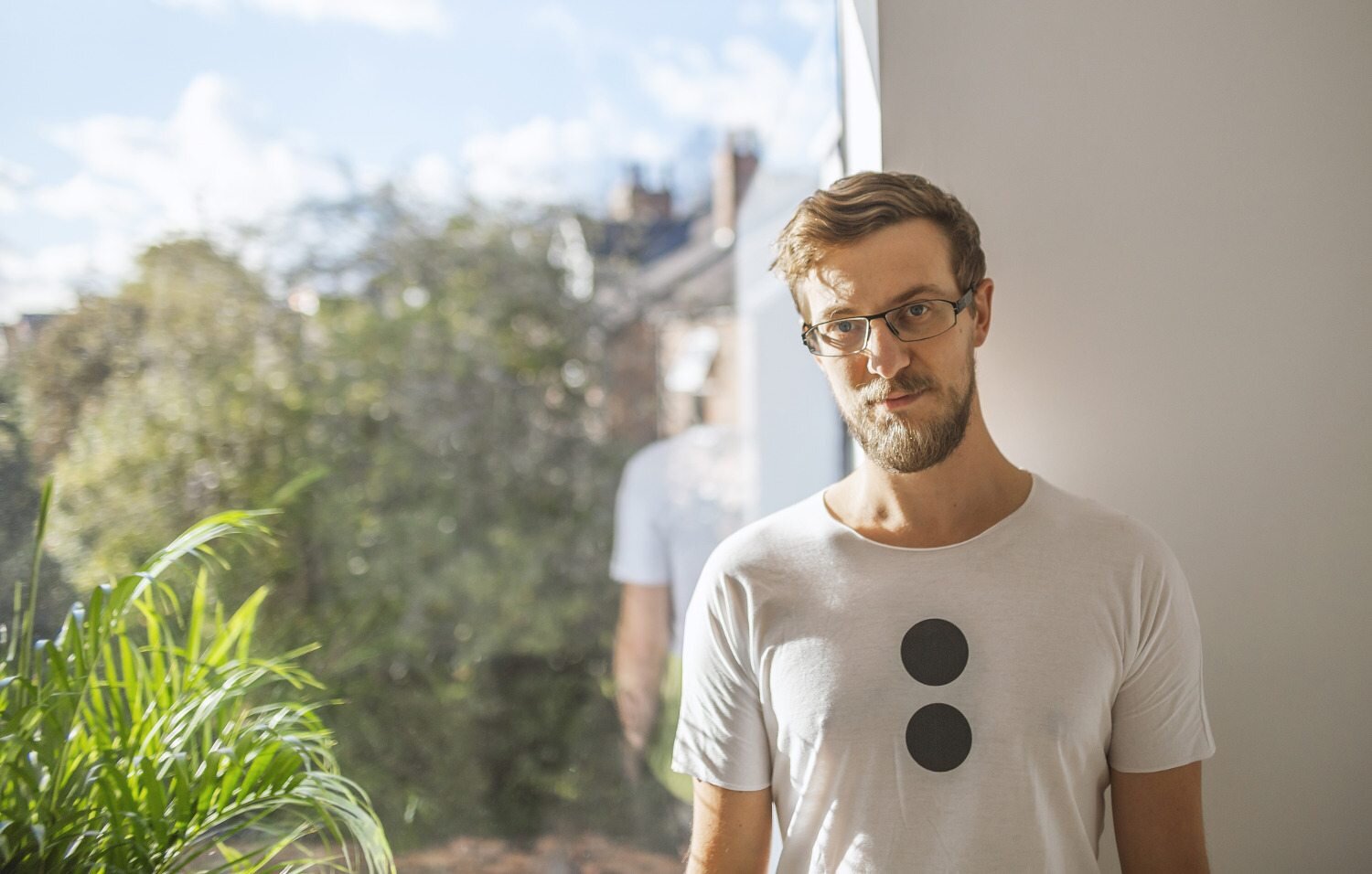
How Kit Knowles is pushing the envelope for sustainable construction
The MD of Ecospheric talks about his recent projects & how he achieved his airtightness goals.
Kit Knowles is MD of Ecospheric, who have recently renovated a pair of Victorian Semi-detached homes to EnerPHit Plus standard in Zetland Road, Manchester. Achieving EnerPhit Plus is already a UK first, but Ecospheric has gone much further than that. We met with Kit Knowles to find out more about his business, and what architects and self-builders can learn.
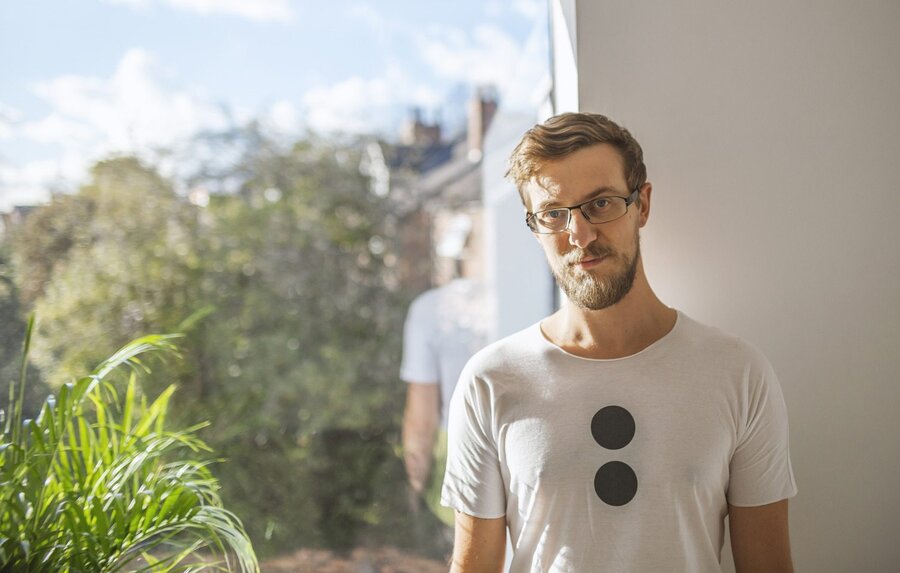
Kit Knowles says that eco-buildings are more than just buildings with mass insulation.
Who is Ecospheric?
Please introduce Ecospheric’s work, what are you up to at the moment?
Kit Knowles (KK): Ecospheric aims to make maximum impact in improving the performance of the built environment through delivering pilot projects and disseminating the learning from those projects. We also design & build innovative high-performance windows and doors. You could say this is work at a local scale.
We don’t work solely in the residential sector. We are designing a zero-waste & ‘zero-energy’ food hall in Manchester. To achieve this starts with the supply chain, itself aiming to be zero waste. To take this across the whole metro area we are discussing with the Greater Manchester Authority on how this can be achieved. We also work with them on new and retrofit housing strategy. This is work at the regional scale.
Finally, at the national scale, we are recording legislative roadblocks and incentives to feed indirectly to Government Department BEIS. This piece of work is open to all. We’re using an innovate platform called Kialo.com to record and structure the debate.
Check out this link where you’ll learn what it is & what isn’t working well at the moment, and contribute to the debate.
“The greenest retrofit ever”
Impressive stuff! What was your motivation for embarking on the Zetland Road scheme?
KK: This is a demonstration project of how far it is possible to go with the retrofit of a period building. We wanted not only to do the ‘greenest retrofit ever’ in embodied and operational energy. We had to make it desirable, too. The product had to look great and fulfill the estate agents ‘golden checklist’.
From a space-planning perspective, a Victorian semi is quite ‘top heavy’. There is plenty of room for the functions on the first and second floors, but there is a lot of pressure on the ground floor. Here is the kitchen, three receptions, WC, utility, alfresco living format with access to the garden and the corridors to connect it all. We applied ‘tiny homes’ principles to make this all work. This meant the fabric and services had to be super compact, too.
There is no extension to the building. Almost all of the onsite materials were reused in some way. The new materials are the lowest possible embodied energy, all-natural and breathable. We’re aiming for petrochemical-free fabric. Membranes, adhesives and fixings are excepted as these are less than 0.1% of the total build and we simply couldn’t have done it without these essential elements.
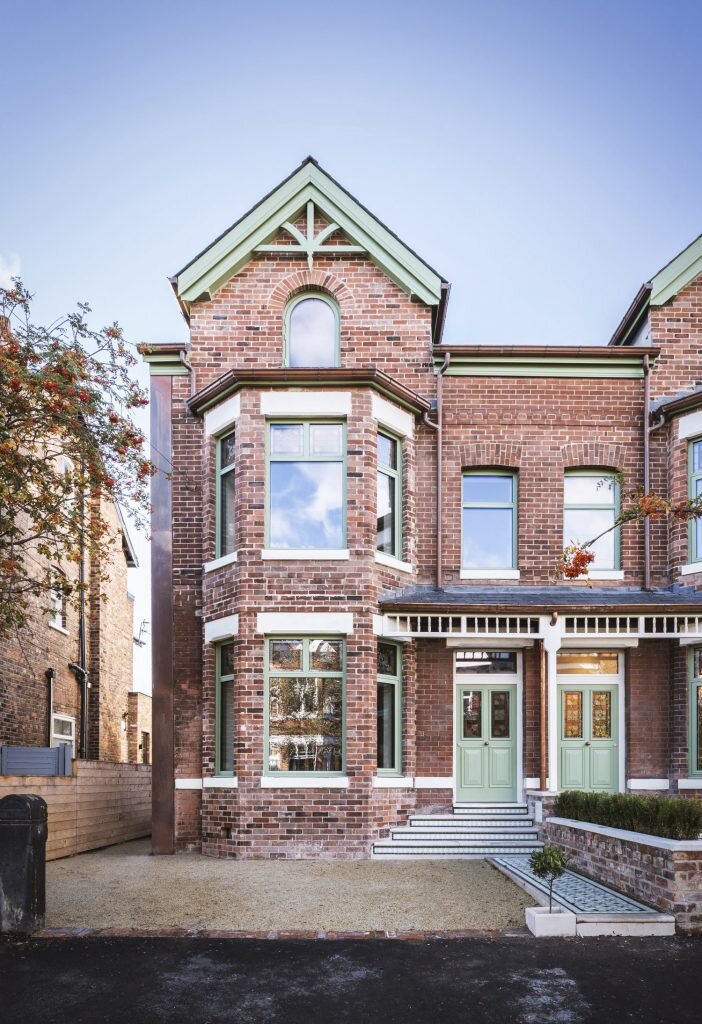
Did you achieve your goals with this project?
KK: We certainly think so! We’ve also achieved eight world firsts (see below), and the building has zero energy bills. We’ve demonstrated scores of new products and details. We’ll share our learning from all this.
What did you apply from your previous projects? What is the context for wider application of the learning from this scheme to the UK ‘hard to heat’ housing stock?
KK: Chorltonville was the very first project, our own self-build renovation, to achieve 80% carbon reduction. We’ve done over 200 projects since then.
Our approach starts with achieving what we call ‘pressure neutrality’ by eliminating one-way air flows. These create uncomfortable draughts, cause moisture issues in fabric, poor occupant health and inflate the energy bills. The main causes of these one-way air flows are; powered extract ventilation, chimneys and flues, SVPs, and leakage through the floors and roof. We deal with those and introduce balanced supply & extract MVHR ventilation. That’s how we guarantee comfort for the occupants and the building. Most domestic retrofits are kitchen extensions. These are often poor-performing and highly glazed. Removal of separating walls can cause over heating of the whole ground floor. Five of six sides of a typical extension are external; the surface to volume ratios are awful. Better to stick within the insulated envelope by avoiding extending the building!
Our pragmatic approach to design (tiny house principles) often allows us to simplify the redesign of properties negating the need to extend. We offset the money saved for a wider and deeper retrofit where possible.
At Zetland Road we removed the front of the chimney breasts. Once braced, these form three vertical risers. This means no more uncontrolled air flow up the chimney. The vertical services distribution is efficient to run and, as it is highly compact, it looks great too. We will certainly be using that strategy again.
The PHPP analysis & airtightness target
How did you achieve 0% summer overheating in the PHPP analysis?
(PHPP is the comfort & energy analysis spreadsheet for Passivhaus & EnerPHit)
KK: Wherever possible we have exposed the existing brick; there’s 200 tonnes of it between the two houses. That helps mediate the temperature fluctuation, although PHPP undervalues this, in my opinion.
Then, there is a careful balance of the glazing. We had control over the design of the southerly rear elevation. The ground floor has the most glazing, with less and less at first and second floors. This was a deliberate choice to balance direct solar gains with the rising hot air.
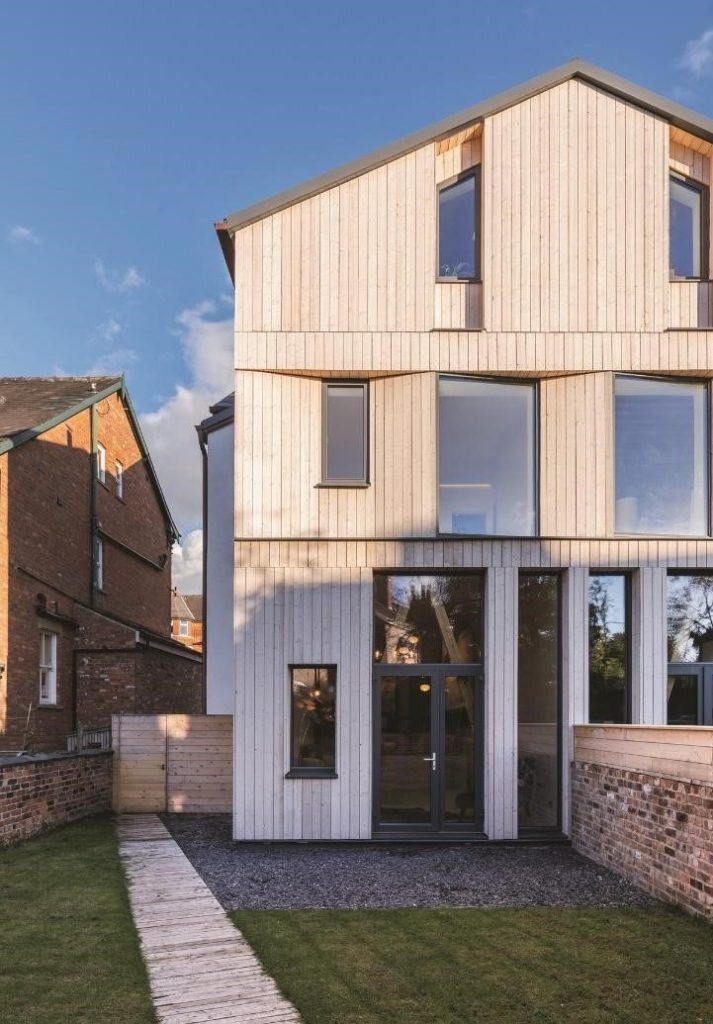
South Elevation showing progressively less glazing from ground, to first, to second floors.
It meant that we had to do some clever interior design tricks on the upper floor to keep it feeling light and airy. For instance, we use plenty of wood as its such low embodied energy, but untreated it can be a sponge for light. By applying white Osmo Raw Hardwax, the floor has a Scandinavian feel which is lovely and bright.
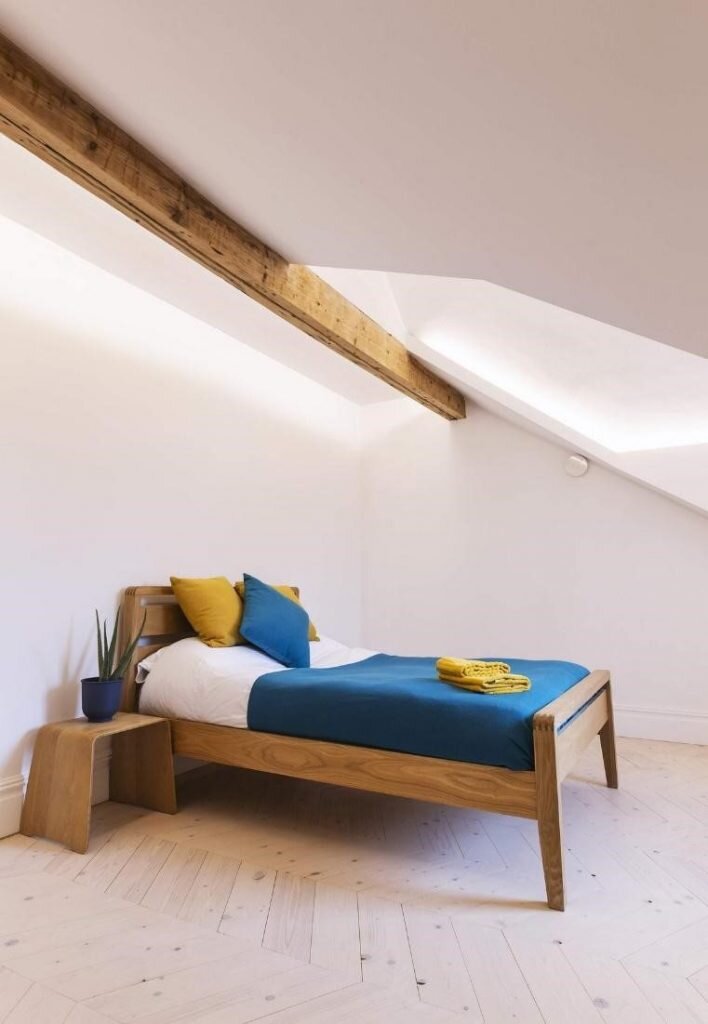
Upper floor showing approach to maximisng available daylight.
Then there are other tricks we employed using internal glazing panels. You’ll have to see it for yourself at the open days coming up.
What airtightness target were you aiming for?
KK: The EnerPHit limit is 1 ACH @50Pa. We’ve achieved 0.78ACH & we are working towards 0.6.
How difficult was that to achieve? In your opinion, can it be replicated, with the right attitude, in widespread retrofit schemes?
KK: Its difficult to get so tight in a period house. As this building is 125 years old, this helps hugely with character and thermal mass; no one would call this a German ‘box’. But most other elements of performance are much harder to come by, in comparison to a new build.
For wider application, well, this is completely dependent upon a retrofit coordinator being appointed to a project to act as an air tightness champion. You must bring airtightness into the design from the off (along with M&E). i.e. at RIBA stage 1 not at 4, as is typical.
The pressure-neutral approach described has could be adopted and rolled out. Whereas airtightness always needs a rigorous and continuous process and duty of care.
Achieving airtightness
How important is good airtightness in the overall scheme?
”When people think of eco-building they simply think masses of insulation. But heat is lost via radiation, conduction and convection.”
KK: Radiation is minor, at around 10%. About 40% of heat loss from a building is via conduction. The insulation will reduce this, directly in proportion to how much insulation you apply.
The other 50% of heat loss is convection. Sorting the air tightness resolves this. But you need a coherent strategy as the air will always take the path of least resistance; don’t expect to be mostly airtight by sealing most of the envelope!
In practice, there are always certain lower hanging fruits available, depending on the specifics of the situation. Keeping an up to date PHPP model allows you to identify where the next easiest improvements are; be they in the insulation, airtightness, services, etc.
What drew you to use SIGA products for many of the details on Zetland Road?
KK: While I don’t approve of over-design in say, structures, I am always looking for belt & braces in moisture control. We’re using SIGA Majrex® in the roof.
This is an intelligent membrane that encourages moisture to leave the insulation under any combination of external and internal conditions. Majrex® is like a one-way valve for moisture. It’s unique and highly effective. It also allows a slimmer roof build up.
The SIGA Sicrall yellow tape is really easy to use. I love how it can be ripped by hand.
You kept the front brick wall and insulated it internally. You included a vented cavity, which must have been a hard concession to make for better moisture control. Could you get away without it on future projects?
KK: We ran multiple calculations and physical tests in order to retain the appearance and deliver risk-free performance. In this case, a slimline cavity was necessary. We are currently working on a monolithic construction detail for a Passivhaus in London.
World firsts for Zetland Road
And finally – here are Ecospheric’s claimed world firsts for the Zetland Road project:
- First stained glass in a Passivhaus
- First petrochemical-free Passivhaus fabric
- Fully breathable fabric, every external wall, floor and roof in a heated home
- EMF free electrical system
- Thermocline control for hot water tank
- Nobel Prize winning material Graphene formulated into the lime paints
- Mono-directional vapour control membrane for lowest risk of interstitial moisture
- Zero Energy Bills for Period Property
- Passivhaus Plus Retrofit (EU-first)
If you wish to dig further into the details of the Zetland Road project, check out this Passivhaus Plus magazine article.
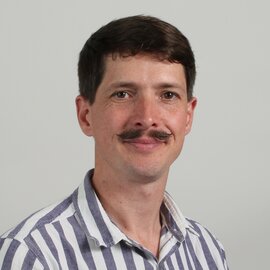
Bertie Dixon
Bertie has practised building services engineering and sustainability consulting in the UK for 15 years. He is a certified PassivHaus planner. He is on a mission to help you deliver a high-quality building, one that does what it says on the tin.